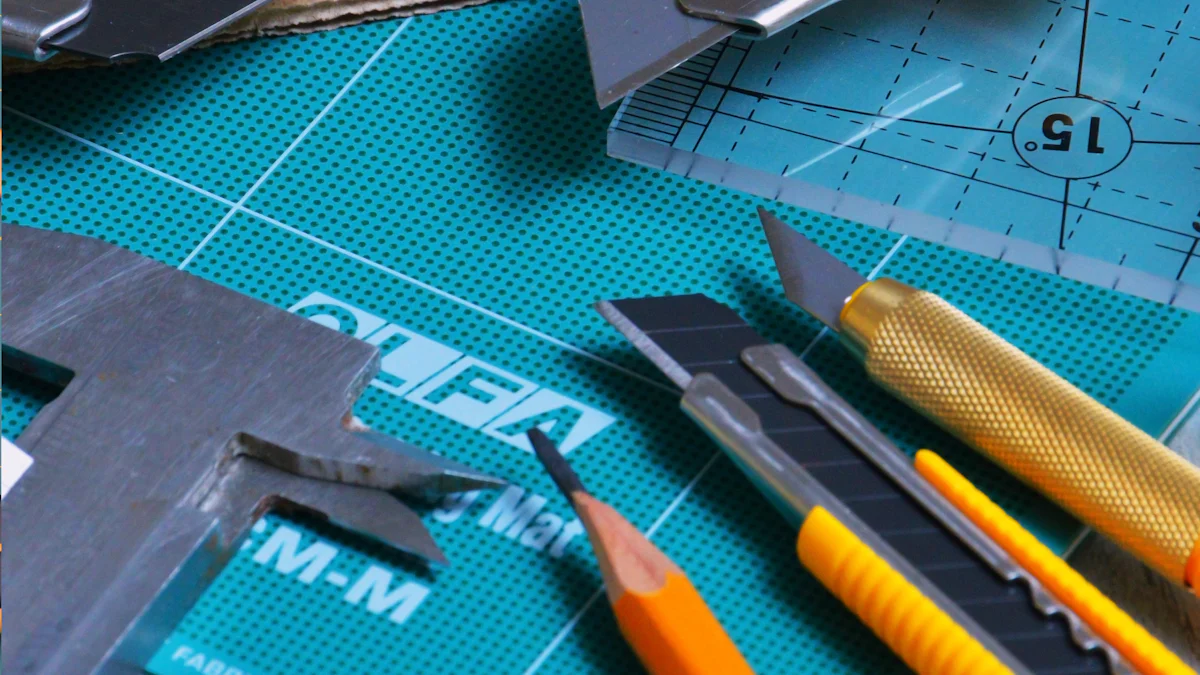
Selecting the right cutting tool holds paramount importance for any project. The market offers a vast array of cut tools, each designed for specific materials and applications. Using the correct tool ensures precision, efficiency, and overall success in your project. Proper set-up and tool choice can prevent issues like chatter, vibration, and distortion, which often lead to subpar results.
Understanding Cutting Tools
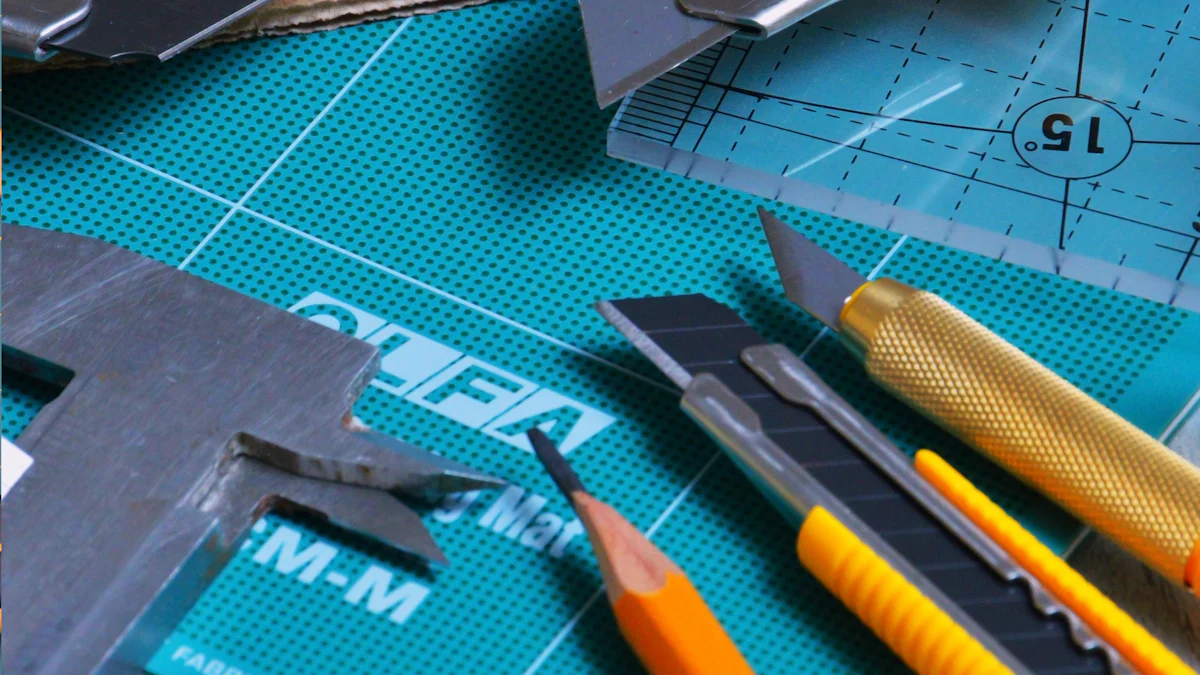
Basic Types of Cutting Tools
Hand Tools
Hand tools include basic cut tools like saws, chisels, and knives. These tools rely on manual effort for operation. Hand tools offer precision and control, making them ideal for detailed work. Common examples include hacksaws for metal cutting and utility knives for general purposes.
Power Tools
Power tools use electricity or batteries to operate. These tools provide higher efficiency and speed compared to hand tools. Examples include electric drills, circular saws, and angle grinders. Power tools are suitable for larger projects requiring more power and speed.
Specialty Tools
Specialty tools cater to specific tasks and materials. These tools include wire cutters, metal snips, and glass cutters. Specialty tools ensure precision and efficiency for unique applications. For instance, wire cutters handle various gauges of wire, while metal snips cut sheet metal like aluminum and steel.
Materials and Their Impact
Tool Material
The material of the cut tool significantly affects its performance. Common materials include high-speed steel (HSS), carbide, and cermet. Monolithic tools, made from a single piece of material, offer rigidity and durability. These tools suit various machining operations like turning, milling, and drilling.
Workpiece Material
The material of the workpiece also influences the choice of cut tools. Hardness, thickness, and composition determine the appropriate tool. For example, softer materials like wood require different tools compared to harder materials like steel. Selecting the right tool material ensures optimal performance and longevity.
Cutting Tool Geometry
Blade Shape
Blade shape plays a crucial role in the efficiency of cut tools. Different shapes cater to various cutting needs. For example, straight blades suit linear cuts, while curved blades handle intricate shapes. Choosing the correct blade shape enhances precision and reduces material waste.
Edge Angle
The edge angle of a cut tool affects its cutting ability and durability. A sharper angle provides a cleaner cut but may wear out faster. Conversely, a blunter angle offers durability but may require more force. Selecting the right edge angle balances sharpness and longevity.
Tooth Configuration
Tooth configuration impacts the cutting performance of tools like saws and blades. Fine-toothed blades offer smooth cuts for delicate materials. Coarse-toothed blades handle tougher materials and faster cutting speeds. Matching the tooth configuration to the material ensures efficient and precise cuts.
Criteria for Selecting Cutting Tools
Project Requirements
Material to be Cut
The material you need to cut plays a crucial role in selecting the right cut tools. Different materials require specific tools to achieve optimal results. For instance, softer materials like wood demand different tools compared to harder materials like steel. High-speed tool steel and carbide are common choices for metal cutting. Diamond and CBN (Cubic Boron Nitride) blades excel in cutting hard materials.
Precision Needed
Precision is another key factor when choosing cut tools. Projects requiring fine details and accuracy need tools that offer high precision. Hand tools like chisels and knives provide excellent control for detailed work. Power tools with adjustable settings also allow for precise cuts. Always match the tool’s precision capabilities with your project’s requirements.
Speed of Cutting
The speed at which you need to complete the cutting task is essential. Power tools generally offer higher speeds compared to hand tools. For large-scale projects, electric drills and circular saws provide the necessary speed and efficiency. However, for intricate tasks, slower speeds may yield better results. Consider the balance between speed and precision for your specific project.
Tool Characteristics
Durability
Durability is a critical characteristic of cut tools. Tools made from high-quality materials like carbide and cermet offer long-lasting performance. These materials withstand wear and tear, ensuring the tool remains effective over time. Durable tools reduce the need for frequent replacements, saving both time and money.
Ease of Use
Ease of use significantly impacts the efficiency of your work. Ergonomically designed tools reduce fatigue and increase productivity. Features like comfortable grips and lightweight designs enhance user experience. Always test tools before purchase to ensure they meet your comfort and usability standards.
Maintenance Needs
Maintenance is essential for keeping cut tools in optimal condition. Tools with simple maintenance requirements save time and effort. Regular sharpening and proper storage extend the life of your tools. Always follow the manufacturer’s guidelines for maintenance to ensure longevity and performance.
Cost Considerations
Initial Cost
The initial cost of cut tools varies widely based on quality and functionality. High-end tools made from premium materials like diamond or CBN come with a higher price tag. However, these tools often offer superior performance and durability. Budget constraints may influence your choice, but investing in quality tools can lead to better results.
Long-term Value
Long-term value should also be a consideration when selecting cut tools. Tools with higher initial costs may offer better long-term value due to their durability and performance. Consider the total cost of ownership, including maintenance and replacement costs. Investing in high-quality tools can provide significant savings over time.
Practical Tips for Selection
Comparing Different Tools
Pros and Cons
Evaluating the pros and cons of various cut tools helps make informed decisions. Hand tools offer precision and control but require more manual effort. Power tools provide speed and efficiency but may lack the finesse needed for detailed work. Specialty tools excel in specific tasks but might not be versatile. Weighing these factors ensures the right tool choice for your project.
User Reviews
User reviews offer valuable insights into the performance and reliability of cut tools. Online platforms and forums provide firsthand experiences from other users. Positive reviews often highlight durability and ease of use. Negative reviews can reveal potential issues like frequent maintenance needs or poor performance. Considering user feedback helps avoid common pitfalls and select the best tool.
Testing Tools Before Purchase
Demo Sessions
Demo sessions allow hands-on experience with cut tools before making a purchase. Many retailers offer demo sessions to showcase their products. Testing tools in a real-world setting helps assess their performance and suitability. Pay attention to factors like comfort, ease of use, and cutting efficiency during these sessions.
Return Policies
Understanding return policies is crucial when purchasing cut tools. Retailers with flexible return policies provide peace of mind. If a tool does not meet expectations, a good return policy allows for an exchange or refund. Always check the terms and conditions of return policies before finalizing a purchase.
Consulting Experts
Professional Advice
Seeking professional advice enhances the selection process for cut tools. Industry experts possess extensive knowledge about various tools and their applications. Consulting professionals helps identify the most suitable tools for specific projects. Expert advice often leads to better tool choices and improved project outcomes.
Online Forums and Communities
Online forums and communities serve as valuable resources for selecting cut tools. These platforms host discussions and reviews from experienced users. Engaging with these communities provides access to diverse opinions and recommendations. Participating in online forums helps gather comprehensive information and make informed decisions.
Advanced Techniques and Safety
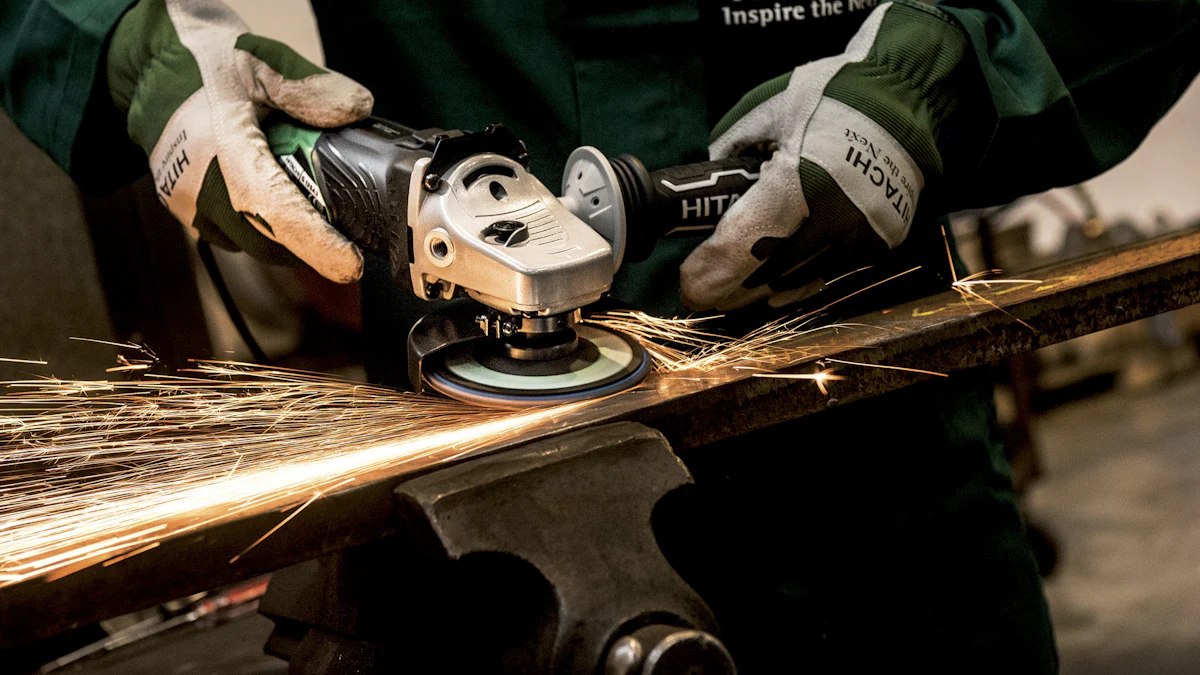
Advanced Cutting Techniques
Precision Cutting
Precision cutting involves techniques that achieve high accuracy and fine details. Ultrasonic vibration-assisted (UVA) cutting stands out for its ability to handle various textures with minimal contamination. UVA cutting reduces cutting force and energy consumption, making it efficient and environmentally friendly. Laser cutting offers another precise method, using focused light to cut materials with extreme accuracy. This technique suits applications requiring intricate designs and minimal material waste. Waterjet cutting uses high-pressure water to cut through materials, providing clean edges without generating heat. These advanced methods enhance the precision of cut tools, ensuring superior results.
Speed Cutting
Speed cutting focuses on completing tasks quickly without compromising quality. Plasma cutting exemplifies this approach by using ionized gas to melt and remove material rapidly. This technique excels in cutting metals like steel, aluminum, and copper. Plasma cutting offers high speed and precision, making it ideal for industrial applications. Another method, high-speed machining, utilizes advanced cut tools made from durable materials like carbide. These tools maintain their sharpness at high speeds, allowing for efficient material removal. Speed cutting techniques improve productivity and reduce project timelines.
Safety Measures
Personal Protective Equipment (PPE)
Personal protective equipment (PPE) is essential when using cut tools. PPE includes items like safety goggles, gloves, and face shields. Safety goggles protect your eyes from debris and sparks. Gloves provide a barrier against cuts and abrasions. Face shields offer additional protection for your face and neck. Always wear appropriate PPE to minimize the risk of injury during cutting operations.
Safe Handling Practices
Safe handling practices are crucial for preventing accidents and ensuring the longevity of cut tools. Always inspect tools before use to check for damage or wear. Store tools in a clean, dry location to prevent rust and corrosion. Use guards or covers for cutting edges when not in use. Follow the manufacturer’s guidelines for tool maintenance and operation. Proper handling and storage extend the life of your tools and keep you safe during use.
Selecting the right cutting tool is crucial for achieving economic machining and delivering high-quality products. Consider factors like material to machine, power available on the machine, fixture stability, and machine dynamics. Choose wisely to ensure precision, efficiency, and project success. The right tool enhances performance and saves time and cost. Always prioritize the correct cutting tool for optimal results.