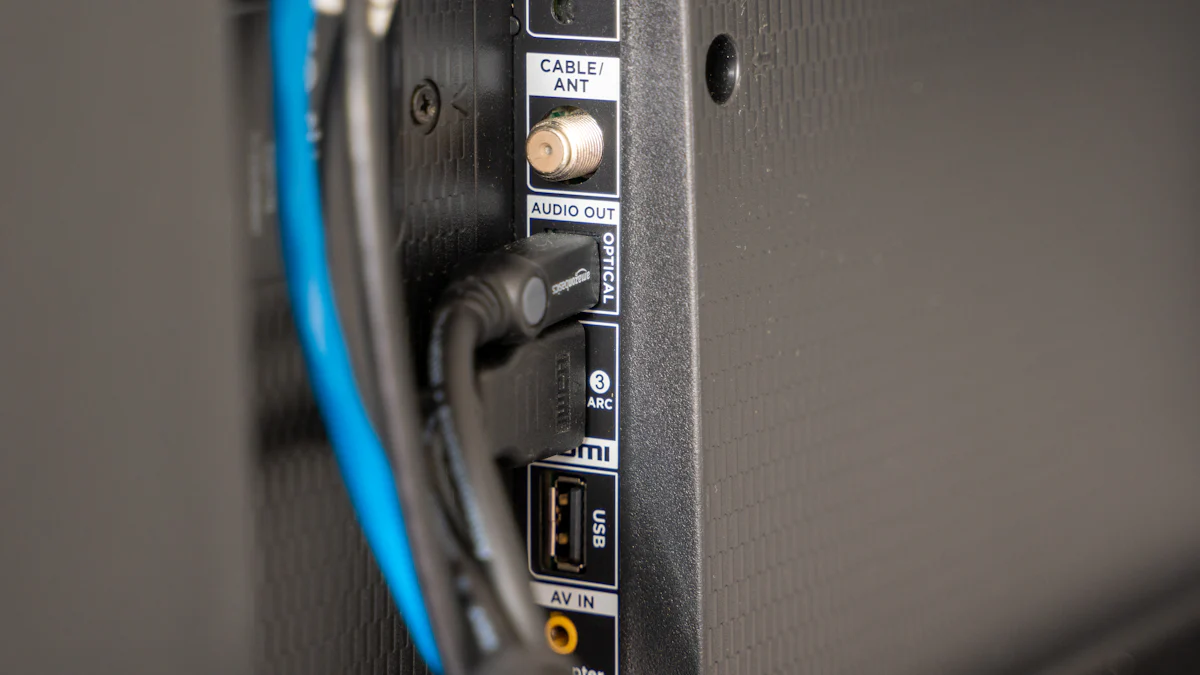
Proper use of an SMA torque spanner ensures the longevity and performance of SMA connectors. These connectors, essential in RF and microwave systems, require precise torque application to function correctly. Incorrect torque can lead to poor connections, signal loss, or even damage to the connectors. Properly torqued SMA connectors can achieve up to 500 mating cycles, making the correct use of a torque spanner crucial for maintaining system reliability.
Understanding SMA Torque Spanners
What is an SMA Torque Spanner?
Definition and purpose
An SMA torque spanner is a specialized tool designed to apply a precise amount of torque to SMA connectors. Proper torque application ensures that the connectors achieve optimal performance without causing damage. The spanner helps maintain the integrity of the connection, preventing issues such as signal loss or mechanical failure.
Key components and design features
An SMA torque spanner consists of several key components. The handle provides a comfortable grip for the user. The torque mechanism ensures that the correct amount of force is applied. The head of the spanner fits securely onto the SMA connector, allowing for precise torque application. Some spanners include a calibration feature to ensure accuracy over time.
Types of SMA Torque Spanners
Fixed vs. Adjustable
Fixed SMA torque spanners come with a preset torque value. These spanners are ideal for applications requiring a consistent torque setting. For instance, a fixed spanner set to 0.5 Nm works well for brass SMA connectors. Adjustable SMA torque spanners allow users to change the torque setting. This flexibility makes them suitable for various types of connectors, including both brass and stainless steel.
Manual vs. Digital
Manual SMA torque spanners require the user to apply force manually until the desired torque is reached. These spanners are simple and reliable, often used in field applications. Digital SMA torque spanners feature electronic displays that show the exact torque being applied. These spanners offer higher precision and are useful in laboratory settings where accuracy is paramount.
Preparing for Use
Selecting the Right Torque Spanner
Factors to consider
Choosing the correct SMA torque spanner involves several factors. First, consider the material of the SMA connectors. Brass connectors require a different torque setting compared to stainless steel connectors. Brass connectors typically need a torque setting of 0.3 to 0.6 N·m. Stainless steel connectors require a higher setting, usually between 0.8 to 1.1 N·m.
Next, evaluate the environment where the SMA torque spanner will be used. Field applications often benefit from manual spanners due to their simplicity and reliability. Laboratory settings may require digital spanners for higher precision. The frequency of use also plays a role. Frequent use may necessitate a more durable and high-quality spanner.
Finally, assess the budget. Prices for SMA torque spanners can vary significantly. High-end models offer advanced features but come at a higher cost. More affordable options may lack some features but still provide adequate performance for less demanding applications.
Compatibility with SMA connectors
Ensuring compatibility between the SMA torque spanner and the connectors is crucial. The spanner must fit securely onto the connector to apply the correct torque. A 5⁄16 inch torque wrench is commonly used for SMA connectors. This size ensures a proper fit and effective torque application.
Different types of SMA connectors may require specific spanners. For instance, right-angle SMA connectors need an 8-inch-pound torque wrench to prevent the connector body from rotating. Always verify the specifications of both the spanner and the connectors to ensure compatibility.
Calibration and Testing
Importance of calibration
Calibration ensures that the SMA torque spanner applies the correct amount of force. Over time, spanners can lose accuracy due to wear and tear. Regular calibration maintains the tool’s precision, ensuring reliable performance. Proper calibration prevents under-torquing or over-torquing, which can lead to poor connections or damage.
Calibration also extends the lifespan of both the spanner and the connectors. Accurate torque application reduces stress on the connectors, preventing premature wear. This practice enhances the overall reliability of the system.
Steps for proper calibration
Calibrating an SMA torque spanner involves several steps:
- Initial Inspection: Check the spanner for any visible damage or wear. Replace any worn-out parts before proceeding.
- Setup: Secure the spanner in a calibration fixture. Ensure the fixture holds the spanner firmly in place.
- Apply Known Torque: Use a calibrated weight or another reference tool to apply a known torque value to the spanner.
- Adjust the Spanner: Compare the applied torque with the spanner’s reading. Adjust the spanner’s calibration mechanism to match the known torque value.
- Verify Accuracy: Repeat the process several times to ensure consistent readings. Make further adjustments if necessary.
Regular calibration checks should be part of the maintenance routine. Periodic recalibration ensures the SMA torque spanner remains accurate over time.
Step-by-Step Guide to Using an SMA Torque Spanner
Initial Setup
Inspecting the spanner and connector
Before using an SMA torque spanner, inspect the tool and the connector. Ensure the spanner has no visible damage or wear. Check the connector for any signs of dirt, debris, or damage. Clean both the spanner and the connector if necessary. A clean and undamaged setup ensures accurate torque application.
Setting the desired torque value
Set the desired torque value on the SMA torque spanner. Refer to the specifications of the connector. Brass SMA connectors typically require a torque setting between 0.3 to 0.6 N·m. Stainless steel connectors need a higher setting, usually between 0.8 to 1.1 N·m. Adjust the spanner to match the required torque value. Ensure the setting is precise to avoid under-torquing or over-torquing.
Applying Torque
Positioning the spanner correctly
Position the SMA torque spanner correctly on the connector. Align the head of the spanner with the connector’s fitting. Ensure a secure fit to prevent slipping during torque application. Proper positioning guarantees that the correct amount of force is applied evenly.
Applying torque evenly
Apply torque evenly using the SMA torque spanner. Turn the spanner slowly and steadily. Avoid sudden movements or jerks. Continue applying torque until the spanner indicates that the desired torque value has been reached. Even torque application prevents damage to the connector and ensures a reliable connection.
Post-Application Checks
Verifying the connection
After applying torque, verify the connection. Check that the connector is securely fastened. Ensure there is no looseness or play in the connection. A secure connection confirms that the correct torque was applied.
Inspecting for any damage
Inspect the connector and the surrounding area for any damage. Look for signs of stress, cracks, or deformation. Address any issues immediately to prevent future problems. Regular inspections maintain the integrity of the system and extend the lifespan of the connectors.
Best Practices and Tips
Maintenance of the Torque Spanner
Regular cleaning and storage
Regular maintenance ensures the longevity and accuracy of an SMA torque spanner. Cleaning the tool after each use removes dirt and debris that can affect performance. Use a soft cloth to wipe down the handle and head. Avoid using harsh chemicals that could damage the tool’s components.
Proper storage also plays a crucial role in maintaining the spanner. Store the tool in a dry, cool place to prevent rust and corrosion. A dedicated case or toolbox provides additional protection. Keeping the spanner in good condition ensures consistent torque application and extends its lifespan.
Periodic recalibration
Periodic recalibration maintains the accuracy of the SMA torque spanner. Over time, the tool can lose precision due to regular use. Schedule recalibration checks based on the manufacturer’s recommendations. Some spanners may require recalibration every six months, while others might need it annually.
Calibration involves adjusting the tool to match a known torque value. This process ensures that the spanner applies the correct amount of force. Accurate torque application prevents damage to SMA connectors and maintains system reliability.
Common Mistakes to Avoid
Over-torquing or under-torquing
Applying incorrect torque can lead to several issues. Over-torquing can damage the connector and reduce its lifespan. Under-torquing can result in loose connections and signal loss. Always refer to the connector’s specifications for the correct torque setting. For example, brass SMA connectors typically require 0.3 to 0.6 N·m, while stainless steel connectors need 0.8 to 1.1 N·m.
Using a torque spanner with a preset value helps avoid these mistakes. For instance, a spanner set to 4 in-lb ensures proper tightening of Halo Connect antenna cables. Consistent torque application prevents loosening and maintains optimal performance.
Using the wrong type of spanner
Choosing the wrong type of torque spanner can compromise the connection. Fixed spanners provide a consistent torque setting, ideal for specific applications. Adjustable spanners offer flexibility for various connector types. Manual spanners are suitable for field use, while digital spanners provide higher precision for laboratory settings.
Ensure compatibility between the spanner and the connector. A 5⁄16 inch torque wrench fits most SMA connectors. Right-angle SMA connectors require an 8-inch-pound torque wrench to prevent rotation. Verify the specifications to select the appropriate tool for the job.
By following these best practices and avoiding common mistakes, users can ensure the proper use of SMA torque spanners. Proper maintenance and accurate torque application enhance the reliability and performance of SMA connectors.
Proper usage of an SMA torque spanner ensures the longevity and performance of SMA connectors. Accurate torque application prevents damage and maintains signal integrity. Users should follow best practices for selecting, calibrating, and maintaining their tools. Regular inspections and proper torque settings enhance system reliability.
“Proper torquing of threaded RF coaxial connectors is essential for reliable, maximum performance interfaces.”
Users are encouraged to share feedback and experiences. Personal insights help improve understanding and application. Community knowledge fosters better practices and tool usage.
See Also
Scooter Upgrades: High-Quality Parts for Optimal Performance
Men and Women’s Sock Selection: A Diverse Range