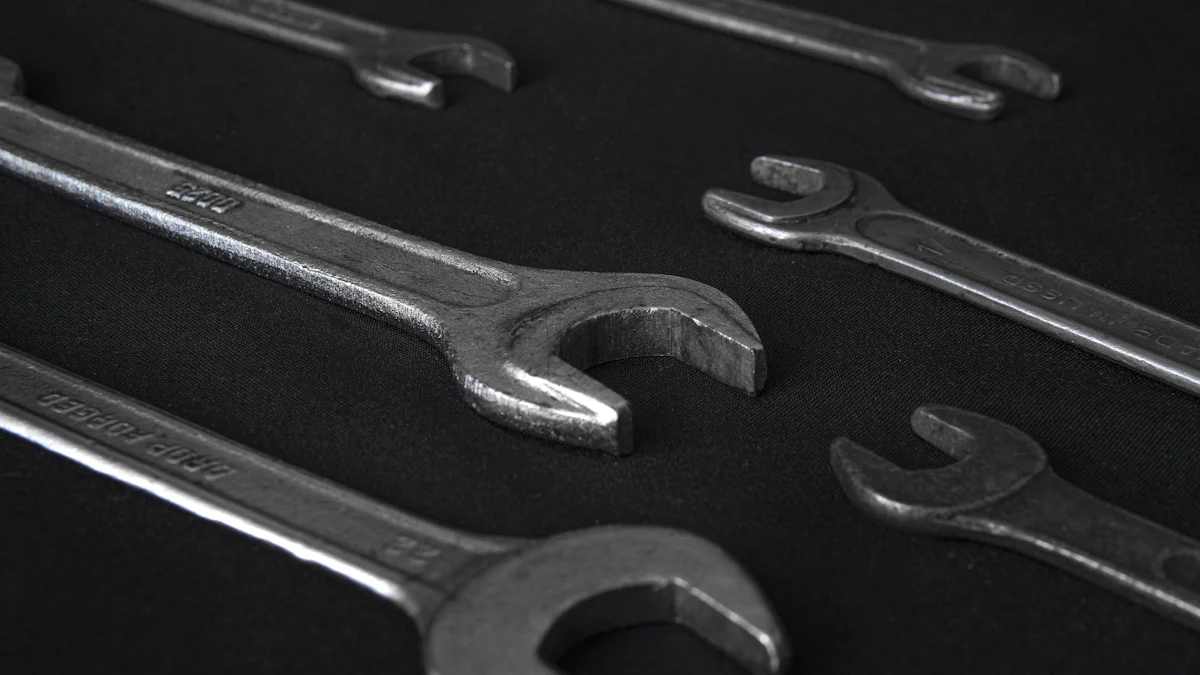
Precision in mechanical work ensures safety, efficiency, and longevity of equipment. A torque wrench plays a crucial role in achieving this precision by applying a specific amount of force to fasteners. Using a torque wrench correctly prevents over-tightening or under-tightening, which can lead to equipment failure or damage. Proper usage of a torque wrench also extends the lifespan of both the tool and the components it services, making it an invaluable asset for any mechanic or technician.
Understanding Torque Wrenches
Types of Torque Wrenches
Click Type
A click type torque wrench provides an audible click when the desired torque value is reached. This type offers simplicity and reliability, making it popular among mechanics. The click sound ensures that users stop applying force at the correct moment, preventing over-tightening.
Beam Type
A beam torque wrench uses a lever arm that bends against a scale to show the applied torque. The analog scale moves with a needle pointer to give a reading. This type does not require calibration as often as other types, providing durability and consistent performance.
Digital Type
A digital torque wrench features internal strain gauges connected to an electronic display. This display shows the current or peak torque value applied to the wrench. Digital wrenches offer higher accuracy but can go out of tolerance if over-torqued.
How Torque Wrenches Work
Basic Mechanics
A torque wrench measures the amount of force applied to a fastener. The tool ensures that bolts and screws are tightened to the manufacturer’s specifications. The mechanics involve either a mechanical or electronic system that translates applied force into a readable torque value.
Calibration Importance
Calibration maintains the accuracy of a torque wrench. Regular calibration checks ensure the tool provides precise readings. Without proper calibration, the wrench may give incorrect torque values, leading to potential equipment failure or damage.
Preparing for Precision
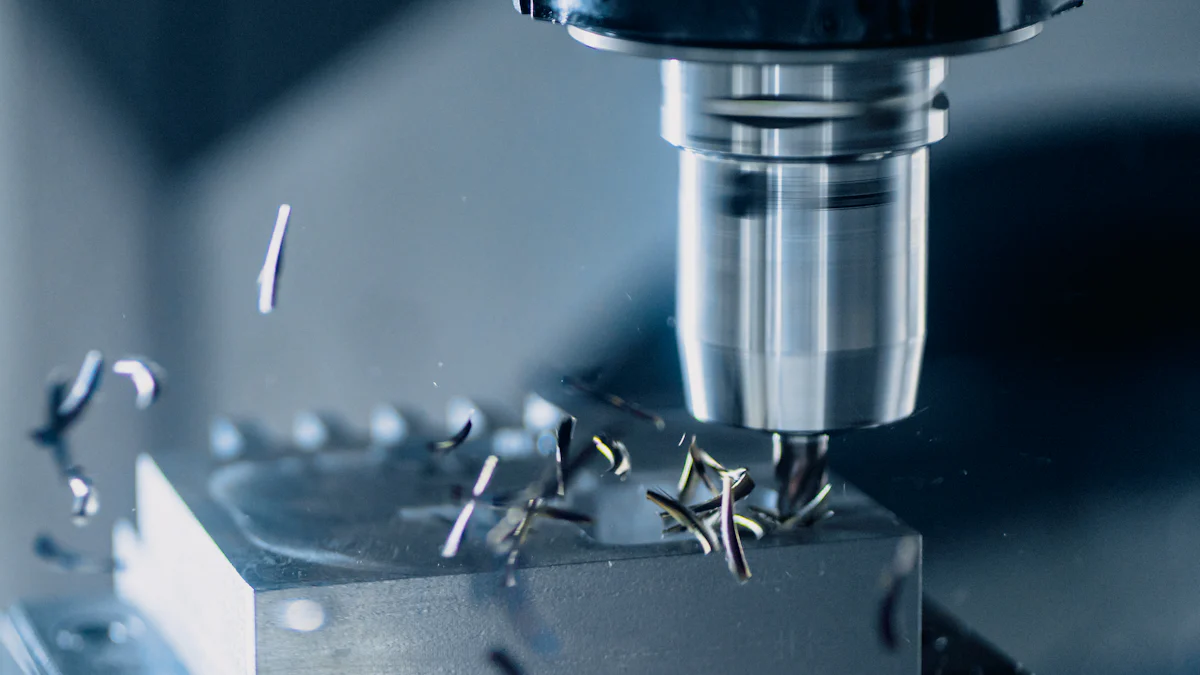
Selecting the Right Torque Wrench
Considering the Task
Choosing the appropriate torque wrench begins with understanding the specific task. Different applications require different torque ranges and precision levels. For instance, automotive repairs often need a click type torque wrench due to its reliability and ease of use. On the other hand, delicate tasks like assembling electronic devices might benefit from a digital torque wrench for its higher accuracy. Assessing the task ensures the selected tool matches the job requirements, enhancing both safety and efficiency.
Matching Specifications
Matching the specifications of a torque wrench to the task at hand is crucial. Each wrench has a specific torque range, typically indicated on the tool. Selecting a wrench with a working range that falls near the midpoint of its capacity guarantees accurate and reliable results. Avoid using wrenches rated below 20% of their full scale, as they may not provide precise torque application. Ensuring the tool meets the required specifications prevents over-tightening or under-tightening, which can lead to equipment failure or damage.
Calibrating Your Torque Wrench
Frequency of Calibration
Regular calibration of a torque wrench maintains its accuracy. The frequency of calibration depends on the usage and the manufacturer’s recommendations. For professional mechanics, calibrating the tool every six months or after 5,000 cycles is advisable. Less frequent users might calibrate annually. Regular checks ensure the wrench provides precise readings, preventing potential equipment failure or damage due to incorrect torque values.
Calibration Methods
Several methods exist for calibrating a torque wrench. One common method involves using a calibration device that measures the applied torque and compares it to the wrench’s reading. Adjustments are made until the wrench provides accurate readings. Another method includes sending the tool to a professional calibration service. This option ensures the wrench meets industry standards and maintains its precision. Proper calibration methods enhance the tool’s performance and longevity, making it an indispensable asset for any mechanic or technician.
Using Your Torque Wrench Correctly
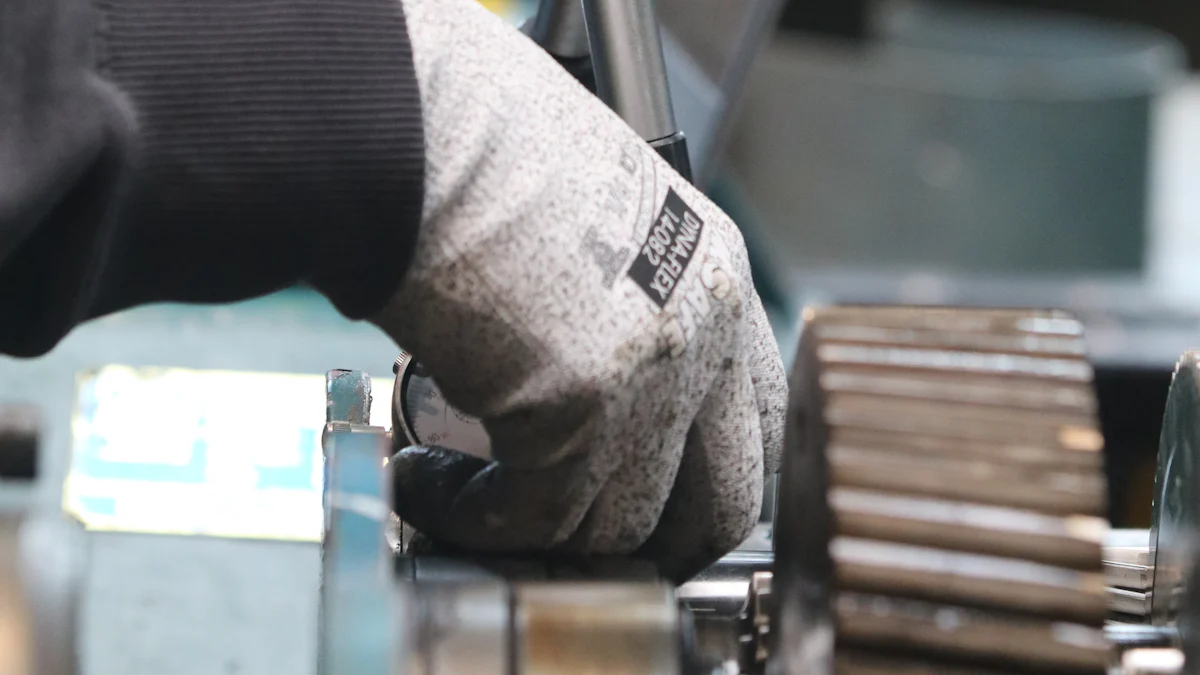
Setting the Desired Torque
Reading the Scale
Reading the scale on a torque wrench requires precision. First, locate the primary scale on the handle. This scale displays the torque values in units such as foot-pounds or Newton-meters. Ensure the wrench is set to zero before starting. Align the zero mark with the main scale to prepare for adjustment.
Adjusting the Wrench
Adjusting the torque wrench involves rotating the handle. Turn the handle until the desired torque value aligns with the reference point. Secure the setting by tightening the lock nut. This step prevents accidental changes during use. Always double-check the setting to confirm accuracy.
Applying Torque
Proper Technique
Applying torque correctly ensures safety and precision. Hold the torque wrench at the pivot point with one hand. Use the other hand to apply force at a 90-degree angle to the handle. Listen for the click sound or observe the digital display. Stop applying force immediately after reaching the desired torque. This method prevents over-tightening.
Avoiding Common Mistakes
Avoid common mistakes when using a torque wrench. Never use the tool for loosening bolts. This action can damage the calibration. Do not exceed the wrench’s capacity. Overloading the tool reduces its accuracy. Store the wrench properly after each use. Improper storage affects its performance. Regularly calibrate the wrench to maintain precision.
Maintenance and Storage
Cleaning Your Torque Wrench
After Each Use
Cleaning a torque wrench after each use ensures its longevity and accuracy. Wipe down the tool with a clean, dry cloth to remove any dirt or debris. Avoid using water or harsh chemicals, as these can damage the wrench. Inspect the wrench for any signs of wear or damage. Addressing minor issues immediately prevents larger problems later.
Periodic Deep Cleaning
Periodic deep cleaning enhances the performance of a torque wrench. Disassemble the wrench according to the manufacturer’s instructions. Use a soft brush to clean internal components. Apply a light coat of lubricant to moving parts to ensure smooth operation. Reassemble the wrench carefully, making sure all parts fit correctly. Regular deep cleaning maintains the tool’s accuracy and extends its lifespan.
Storing Your Torque Wrench
Ideal Storage Conditions
Proper storage conditions preserve the accuracy of a torque wrench. Store the wrench in a clean, dry place to prevent rust and corrosion. Use a protective case to shield the tool from dust and physical damage. Keep the wrench away from extreme temperatures, as these can affect its calibration. Following these guidelines ensures the wrench remains in optimal condition.
Long-term Storage Tips
Long-term storage requires additional precautions to maintain a torque wrench. Release the tension on the wrench before storing it. This step prevents stress on the internal components. Store the wrench horizontally to avoid bending or warping. Check the wrench periodically, even if not in use, to ensure it remains in good condition. Proper long-term storage practices protect the tool and ensure its readiness for future use.
To achieve precision with a torque wrench, follow the key points outlined in this guide. Select the appropriate wrench for each task. Regularly calibrate the tool to maintain accuracy. Apply the correct technique when using the wrench. Clean and store the wrench properly to ensure longevity.
Practice these steps consistently. Precision in mechanical work enhances safety and efficiency. Proper use of a torque wrench prevents equipment failure and extends the lifespan of components. Invest in quality tools and maintain them well. Precision pays off in the long run.
See Also
Discovering the Assortment of Socks for Males and Females