
Hand welding tools are indispensable for welders at all skill levels. Welding tools play a crucial role in fastening and loosening nuts and bolts, essential for disassembling and assembling metal components. As Ronix Tools emphasizes, chipping hammers are vital for removing slag and metal bits during welding tasks. In this blog, we delve into the significance of mastering these tools, providing insights on their functions, techniques, and benefits.
Mastering the Basics
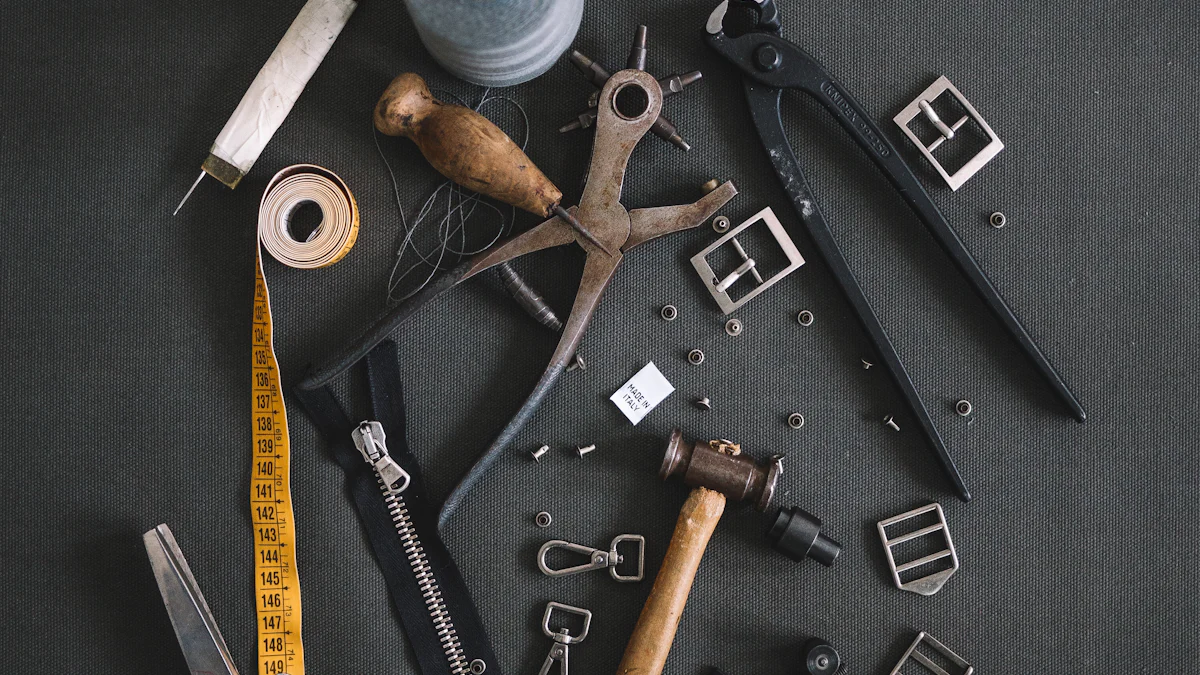
When it comes to hand welding tools, understanding their types and basic functions is essential for any welder.
Understanding Hand Welding Tools
Types of Hand Welding Tools
- MIG welding pliers
- Clamps
- Locking pliers
- Chipping hammers
- Wire brushes
Basic Functions and Uses
- MIG welding pliers are crucial for securely holding metal pieces in place during the welding process.
- Clamps provide stability and alignment for accurate welds.
- Locking pliers ensure a firm grip on materials, preventing slippage while welding.
- Chipping hammers are used to remove excess slag and debris from welded joints.
- Wire brushes help clean metal surfaces before welding, ensuring better adhesion.
Essential Techniques
Proper Handling
To master hand welding tools, proper handling is key. Maintaining a firm grip and using tools with precision enhances the quality of welds.
Basic Welding Methods
Understanding the basic welding methods such as stick welding, MIG welding, and TIG welding is fundamental for beginners. Each method has its unique applications and benefits.
Starting with Simple Projects
Beginner Projects
- Welding two metal plates together to form a simple joint.
- Creating a basic metal sculpture using various welding techniques.
Common Mistakes to Avoid
- Neglecting safety gear like gloves and goggles.
- Ignoring proper ventilation in the workspace can lead to health hazards.
Mastering these basics sets a solid foundation for aspiring welders looking to enhance their skills with hand-held laser welding tools.
Advanced Techniques
Precision and Accuracy
Techniques for Thin Sheets
In the realm of welding, precision and accuracy are paramount, especially when dealing with thin sheets. Welding thin materials requires a delicate touch and meticulous attention to detail. One effective technique is to adjust the welding parameters to suit the thickness of the material. By fine-tuning settings such as heat input and travel speed, welders can achieve clean and precise welds on thin sheets without compromising strength or integrity.
Another strategy for welding thin sheets with precision is to utilize backstepping. This technique involves welding in short segments while moving backward, allowing for better control over heat distribution and minimizing distortion. Additionally, using a lower voltage setting can help prevent burn-through on thinner materials, ensuring a smooth and consistent weld bead.
Welding Different Materials
The versatility of hand welding tools extends to their ability to weld a variety of materials with accuracy. Whether working with stainless steel, aluminum, or titanium, understanding the unique properties of each material is crucial for achieving high-quality welds. For instance, adjusting the shielding gas composition can optimize penetration depth and reduce spatter when welding different metals.
Moreover, employing proper joint preparation techniques such as beveling or chamfering enhances the bonding strength between dissimilar materials. By creating clean and precise joint configurations, welders can ensure strong molecular adhesion between the metals being joined. This meticulous approach results in durable welds that withstand rigorous testing and real-world applications.
Speed and Efficiency
Increasing Welding Speed
In today’s fast-paced manufacturing environment, efficiency is key. Welders can boost their productivity by implementing strategies to increase welding speed without compromising quality. One effective method is to optimize travel speed while maintaining proper arc length and deposition rate. By finding the right balance between speed and heat input, welders can expedite the welding process without sacrificing weld integrity.
Time-Saving Tips
To streamline workflows and save time during welding projects, incorporating time-saving tips can make a significant difference in overall productivity. Utilizing pre-programmed settings on advanced hand-held laser welding systems allows for quick setup and seamless operation. Additionally, leveraging automation features like robotic arms for repetitive tasks minimizes manual labor and accelerates project completion.
By embracing precision techniques for thin sheets and mastering efficient practices for speed and productivity, welders can elevate their craft to new heights of excellence in hand welding tools utilization.
Safety and Maintenance
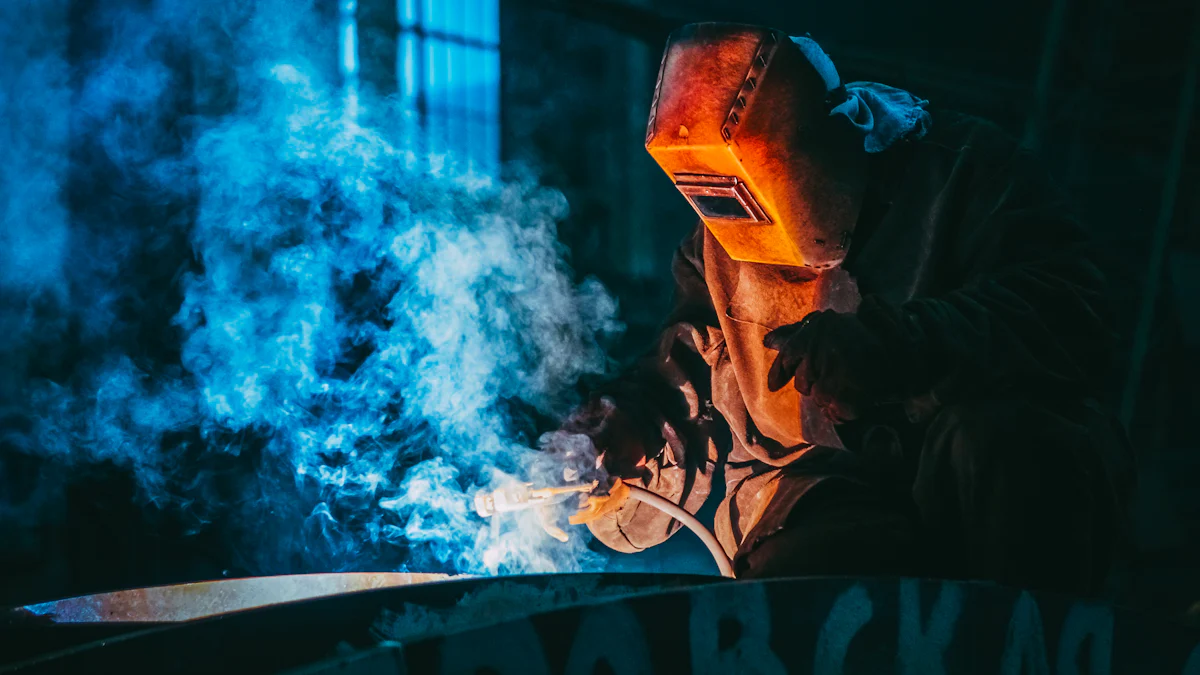
Safety Measures
- Protective Gear: Welders must prioritize safety by wearing appropriate protective gear, including helmets, gloves, and flame-resistant clothing. These items shield the welder from sparks, heat, and UV radiation, ensuring a secure working environment.
- Safe Practices: Adhering to safe welding practices is paramount for accident prevention. Maintaining a clean workspace free of clutter reduces tripping hazards and improves overall efficiency during welding tasks.
Tool Maintenance
- Regular Cleaning: Keeping hand welding tools clean is essential for their longevity and performance. Regularly removing debris and dirt buildup prevents corrosion and ensures smooth operation of the tools.
- Proper Storage: Storing hand welding tools in a dry and secure location protects them from environmental damage. Organizing tools in designated spaces minimizes the risk of misplacement and prolongs their lifespan.
Long-Term Care
- Extending Tool Lifespan: Investing in high-quality hand welding tools not only enhances work quality but also extends the lifespan of the equipment. Proper maintenance practices like lubrication and calibration contribute to prolonged tool durability.
- Professional Maintenance Services: Periodic professional maintenance services can identify potential issues early on, preventing costly repairs or replacements. Engaging experts for tool inspections and tune-ups ensures optimal performance and safety compliance.
By prioritizing safety measures, implementing regular tool maintenance routines, and seeking professional care when needed, welders can maximize the efficiency and longevity of their hand welding tools. Remember, a well-maintained tool is a reliable companion in achieving precision welds and exceptional results in metal fabrication projects.
In reflecting on the journey from novice to pro in mastering hand welding tools, it is essential to recap the key points learned. Welders who have progressed from novice to pro have advanced technical and welding skills, showcasing their dedication to continuous learning and practice. The transformation from a beginner handling basic projects to an expert executing advanced techniques demonstrates the commitment required for excellence in the field. Embrace this journey with enthusiasm and persistence, as each welder’s evolution contributes to the collective expertise of the welding community.