Essential Welding and Metalworking Tools
Importance of Strong Hand Tools in Metalworking
When it comes to metalworking projects, the use of strong hand tools is paramount. These powerful hand instruments play a crucial role in ensuring precision and efficiency throughout the welding process. From cutting and shaping metal to joining and assembling components, sturdy manual tools are indispensable for achieving high-quality results. Additionally, the right welding gear not only enhances productivity but also contributes to a safer work environment. By understanding the significance of robust hand instruments, welders and metalworkers can elevate the quality of their craftsmanship while prioritizing safety.
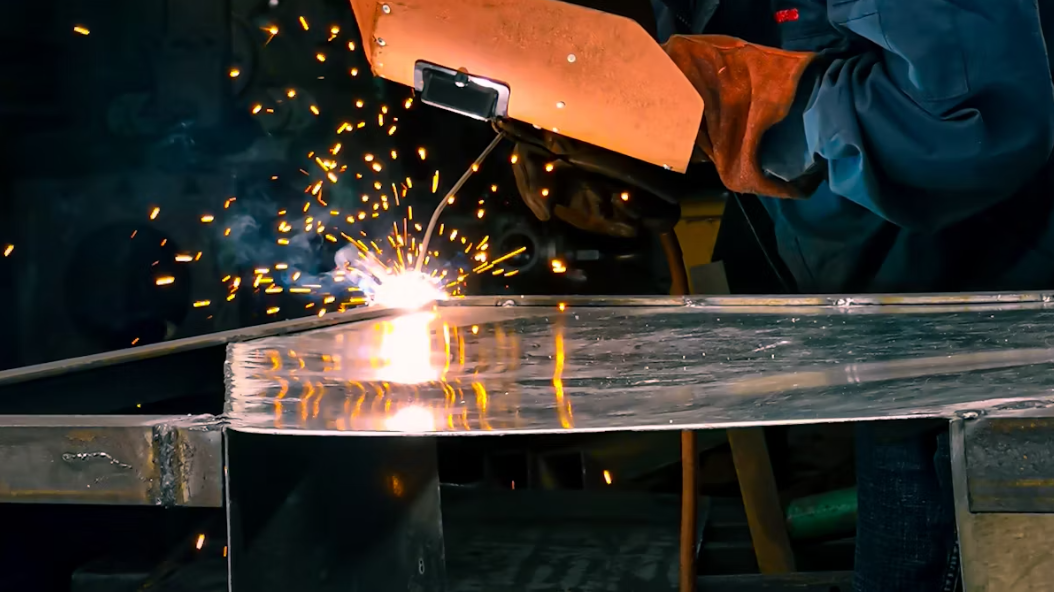
Exploring Various Types of Strong Hand Tools
In metalworking, a diverse range of welding equipment and soldering tools are utilized to meet specific project requirements. Understanding the applications of these joining apparatus allows professionals to select the most suitable tools for their tasks. Whether it’s clamps, vises, hammers, or pliers, each type of strong hand tool serves a unique purpose in metalworking processes.
Safety and Efficiency in Metalworking Projects
Ensuring safety and efficiency in metalworking projects is intrinsically linked to the use of appropriate tools. By employing the right protective gear and selecting the ideal strong hand tools for each task, workers can mitigate risks while optimizing their performance. Adhering to safety guidelines and leveraging efficient welding equipment fosters a productive work environment that prioritizes both quality outcomes and worker well-being.
Exploring Welding Techniques
Arc Welding
Arc welding is a fundamental welding technique commonly used in metalworking projects. This process involves creating an electric arc between the base metal and an electrode, which generates the heat necessary to melt and fuse the metals. One of the key advantages of arc welding is its versatility, as it can be applied to various types of metals, including steel, aluminum, and copper. Additionally, arc welding techniques enable precise control over the welding parameters, allowing for customization based on the specific requirements of each project.
MIG Welding
MIG (Metal Inert Gas) welding, also known as Gas Metal Arc Welding (GMAW), is another widely utilized metal fusion technique in metalworking projects. This method involves feeding a solid wire electrode through a welding gun, along with a shielding gas that protects the weld pool from atmospheric contamination. MIG welding offers several benefits, including high efficiency, speed, and ease of use. Moreover, it is suitable for both thin and thick metal sections, making it a versatile choice for various welding applications.
Understanding Metalworking Processes
Cutting and Shaping
In metalworking, the cutting and shaping processes are essential for transforming raw metal materials into the desired forms for fabrication. Various techniques are employed to achieve precise cutting and shaping, including:
- Shearing: This process involves cutting metal sheets using shear forces, resulting in clean and straight edges. Shearing is commonly used for creating flat components in metal fabrication.
- Milling: Metal milling utilizes rotary cutters to remove material from a workpiece, producing complex shapes and profiles. This method is ideal for creating slots, holes, and intricate designs in metal components.
- Forming: Metal forming techniques such as bending, rolling, and stamping are utilized to shape metals into specific configurations. These methods allow for the creation of curved or angled components that meet project requirements.
The tools and equipment required for precise cutting and shaping of metal include saws, shears, lathes, milling machines, press brakes, and dies. Each tool serves a distinct purpose in achieving accurate dimensions and surface finishes during the cutting and shaping processes.
Joining and Assembling
Metal joining and assembling involve bringing together individual metal components to create a unified structure. Common techniques used for joining metals include:
- Welding: Welding processes such as arc welding, MIG welding, TIG welding, and spot welding are employed to fuse metal parts together securely. Each welding method offers unique advantages based on the specific requirements of the project.
- Brazing: Brazing utilizes a filler material that melts above 840°F (450°C) to join metals without melting the base materials. This technique is suitable for joining dissimilar metals or components with close tolerances.
- Fastening: Fastening methods such as bolting, riveting, and adhesive bonding provide alternative means of joining metal parts when welding or brazing may not be feasible.
Understanding these methods of metal joining is crucial for selecting the appropriate tools such as welding machines, soldering irons, brazing torches, fasteners, adhesives, and clamps to ensure strong and durable assemblies.
Selecting the Ideal Welding Machine
Considerations for Welding Machines
When selecting the ideal welding machine, several key factors should be taken into account to ensure its suitability for specific metalworking projects. Understanding the nature of the welding tasks and the types of metals involved is crucial in making an informed decision. Additionally, considering the power source, portability, and ease of use can significantly impact the overall efficiency and effectiveness of the welding process.
- Power Source: Determine whether a welding machine powered by electricity, gas, or battery is best suited for the project requirements. The availability of power sources at the worksite should also be considered.
- Portability: Assess the mobility needs within the workspace and choose a welding machine that offers convenient portability without compromising performance.
- Ease of Use: Look for user-friendly features such as adjustable settings, clear display interfaces, and ergonomic designs that enhance operational convenience and precision.
Exploring these considerations will help in selecting a welding machine that aligns with the specific demands of metalworking projects, ensuring seamless operations and high-quality results.
Efficiency and Performance
Examining the efficiency and performance attributes of a welding machine is essential for successful metalworking projects. Features such as duty cycle, welding output capabilities, and advanced technologies contribute to enhanced productivity and quality outcomes. Understanding these aspects enables welders to optimize their processes while maintaining safety standards and achieving superior weld integrity.
Efficiency Tip: Investing in a welding machine with higher duty cycles can lead to increased productivity by minimizing downtime during extended welding sessions.
By prioritizing efficiency and performance when choosing a welding machine, metalworkers can elevate their craftsmanship while streamlining their workflow for maximum effectiveness.
Ensuring Safety in Metalworking
Protective Gear and Equipment
When engaging in metalworking projects, the use of protective equipment and safety gear is non-negotiable. Safety attire such as goggles, face shields, and protective gloves are essential for safeguarding against potential hazards during cutting, welding, and shaping processes. Additionally, safety garments like flame-resistant clothing and steel-toed boots provide vital protection against heat, sparks, and heavy materials. The significance of safety gear cannot be overstated, as it not only minimizes the risk of injuries but also promotes a secure working environment conducive to optimal productivity.
Exploring the importance of personal protective equipment (PPE) reveals its critical role in preventing workplace hazards. By donning appropriate safety attire and utilizing protective equipment such as earplugs or earmuffs to mitigate noise exposure, metalworkers prioritize their well-being while upholding industry-standard safety practices.
Safety Guidelines and Practices
Adhering to comprehensive safety guidelines is paramount in metalworking environments. Implementing best practices such as conducting regular equipment inspections, maintaining clean work areas to prevent slips or falls, and providing adequate ventilation for fume extraction ensures a safe working environment. Furthermore, establishing clear protocols for handling hazardous materials and enforcing proper tool usage contributes to minimizing risks.
Providing tips and recommendations for maintaining a safe working environment during metalworking projects includes emphasizing the importance of ongoing safety training for all personnel involved. Encouraging open communication about safety concerns fosters a culture of vigilance where every individual plays an active role in promoting a secure workspace.
Key Strong Hand Tools for Success
Importance of Selecting the Right Tools
Selecting the right strong hand tools is a critical aspect of ensuring success in welding and metalworking projects. Powerful hand tools are essential for achieving precision and efficiency, while sturdy manual tools contribute to the overall quality of craftsmanship. By prioritizing the use of robust hand instruments, metalworkers can elevate their workmanship and enhance project outcomes.
Prioritizing Safety Measures
In addition to choosing the appropriate tools, prioritizing safety measures and utilizing protective gear is paramount in metalworking. Ensuring a secure working environment through the use of safety equipment fosters a culture of well-being and productivity.
Ensuring Efficiency and Precision
Efficiency and precision are fundamental to successful welding and metalworking projects. By employing appropriate welding equipment and strong hand tools, workers can optimize their performance while maintaining high standards of craftsmanship.