Understanding Earth Clamps
Earth clamps play a crucial role in welding techniques, serving as vital components that ensure the safety and effectiveness of the entire welding process. These clamps, also known as ground clamps or welding clamps, are responsible for creating a secure connection between the welding machine and the metal being welded. By providing a stable grounding point, earth clamps help to prevent electrical hazards and ensure that the welder can work with confidence and precision.
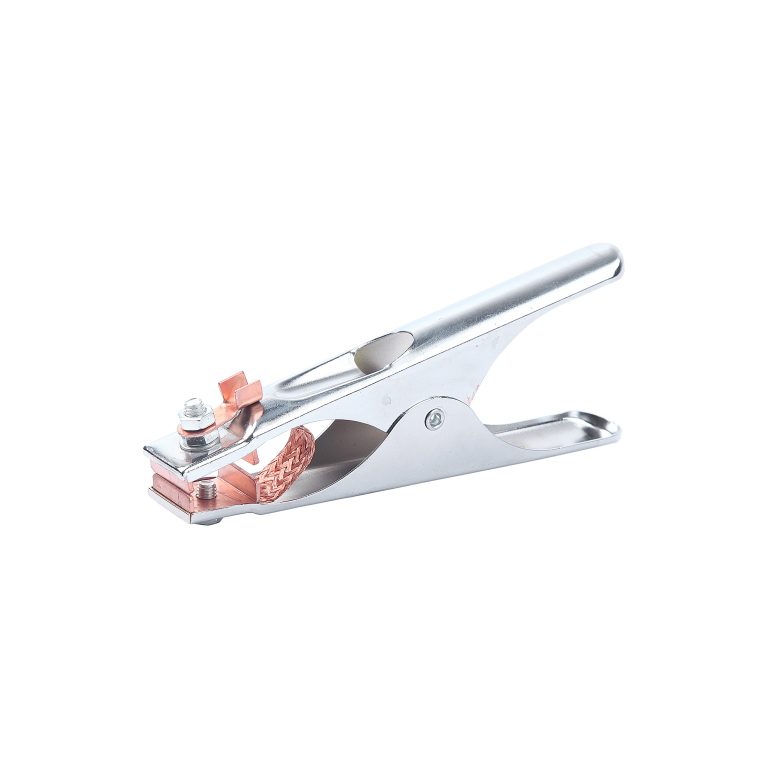
Earth Clamp Varieties
When it comes to welding, different earth clamp designs are tailored to meet various welding needs and applications. Understanding the distinct features and uses of these earth clamp varieties is essential for ensuring welding efficiency.
Types of Earth Clamps
- Screw type: These clamps feature a screw mechanism for securing the connection, offering a versatile option for different workpieces.
- Magnetic type: Equipped with a magnetic base, these clamps provide a convenient solution for quick and easy attachment to ferrous materials.
- Heavy-duty type: Designed to withstand rugged conditions, heavy-duty earth clamps offer durability and stability, making them suitable for demanding welding tasks.
Selecting the Right Earth Clamp
When choosing an earth clamp for specific welding tasks, several factors should be taken into account. The material being welded, the welding technique employed, and the intensity of the electrical current are all crucial considerations. It is important to select the appropriate earth clamp that matches the requirements of different welding techniques, ensuring optimal safety and performance.
Significance of Grounding
Grounding is a critical aspect of welding, playing a pivotal role in ensuring the safety and efficiency of the entire welding process. Proper grounding is essential for preventing electrical hazards and maintaining a secure work environment for welders.
Importance of Grounding in Welding
The significance of grounding in welding cannot be overstated. It serves as a fundamental safety measure, effectively dissipating any stray currents and preventing the risk of electric shock. Additionally, grounding contributes to the overall stability of the welding operation, allowing for consistent and precise welds to be achieved.
Grounding Techniques
In welding, various methods are employed to establish proper grounding. These techniques include direct metal-to-metal contact with the earth, using grounding clamps to create a secure connection between the workpiece and the welding machine, and employing specialized grounding cables. The choice of grounding technique significantly impacts the quality of welds, making it crucial to select the most suitable method for each welding scenario.
By implementing effective grounding techniques, welders can ensure that electrical currents are safely directed away from the work area, thereby minimizing potential risks and enhancing the overall integrity of the welding process.
Diverse Welding Methods
Overview of Welding Techniques
Welding encompasses a diverse range of techniques, each tailored to specific applications in various industries. Some common welding methods include:
- Arc Welding: This method employs an electric arc to create intense heat, fusing metal pieces together. It is widely used in construction, fabrication, and repair work.
- MIG (Metal Inert Gas) Welding: Also known as Gas Metal Arc Welding (GMAW), this process uses a wire electrode and inert gas to shield the weld from atmospheric contamination. MIG welding is versatile and suitable for both thin and thick materials.
- TIG (Tungsten Inert Gas) Welding: TIG welding utilizes a non-consumable tungsten electrode to produce the weld. It is ideal for precision work on thin materials and is commonly used in aerospace and automotive industries.
- Stick Welding: Also known as Shielded Metal Arc Welding (SMAW), stick welding involves a flux-coated electrode that creates the weld. It is favored for its portability and versatility in outdoor or remote locations.
Welding Process Considerations
When selecting a welding technique, several factors must be considered to ensure optimal results:
- Material Thickness: The thickness of the metal being welded influences the choice of welding method. Thicker materials may require processes such as stick welding or flux-cored arc welding, while thinner materials are best suited for TIG or MIG welding.
- Joint Design: The type of joint being welded, whether it’s a butt joint, lap joint, or fillet joint, impacts the selection of the appropriate welding technique.
- Environmental Conditions: Factors such as indoor or outdoor welding, wind conditions, and accessibility can influence the choice of welding process.
The selection of the right earth clamp is closely tied to the chosen welding method. Different techniques may require specific grounding configurations to ensure safety and effectiveness throughout the welding process.
Clamps in Metalworking
Role of Clamps in Metalworking
In the realm of metalworking, clamps play a pivotal role as essential holding devices and fixtures. These clamping tools are instrumental in securing workpieces during various metalworking processes, including welding. The primary function of clamps in metalworking is to firmly hold the materials in place, allowing for precision and stability during cutting, shaping, and joining operations.
Moreover, the relationship between clamps and welding in metalworking applications is integral. During welding processes, clamps are utilized to secure the pieces being welded together, ensuring that they remain in the correct position throughout the operation. This not only contributes to the accuracy of the weld but also enhances safety by preventing movement or misalignment of the workpieces.
The efficiency and effectiveness of metalworking processes heavily rely on the proper utilization of clamps. By securely holding materials in position, these clamping tools facilitate seamless execution of various tasks, ultimately contributing to the overall quality and precision of metalworking operations.
Types of Clamps in Metalworking
Metalworking encompasses a diverse array of clamping tools designed to cater to different requirements. Some common types include:
- C-Clamps: These versatile clamps feature a C-shaped frame and are widely used for securing metalworkpieces to a work surface.
- Bar Clamps: Known for their long adjustable bar design, these clamps provide extended reach and are suitable for larger projects.
- Spring Clamps: Featuring spring-loaded jaws, these lightweight clamps are ideal for securing small or delicate workpieces during intricate metalworking tasks.
- Toggle Clamps: These specialized clamps offer quick and efficient one-handed operation, making them valuable for repetitive holding applications.
The variety of available clamping tools ensures that metalworkers can select the most appropriate type for specific tasks, thereby enhancing productivity and precision in their craft.
Earth Clamp Applications
Earth clamps find diverse applications across various welding techniques, playing a pivotal role in ensuring the safety and effectiveness of the welding process. These clamps, also referred to as ground clamps or welding clamps, are instrumental in establishing a secure connection between the welding machine and the metal being welded. By providing a stable grounding point, earth clamps contribute to preventing electrical hazards and maintaining a secure work environment for welders. Understanding the versatile applications of earth clamps is essential for optimizing their use in different welding scenarios.