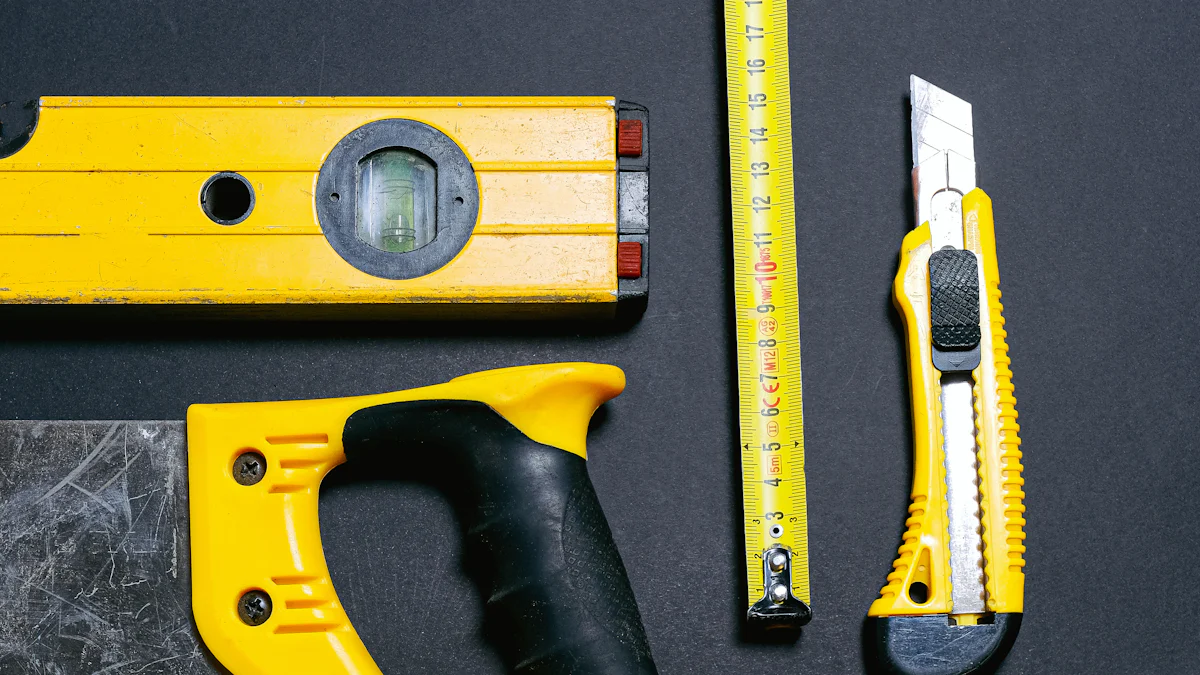
Precision matters when cutting foam. Clean and accurate cuts make a big difference in the final product. Specialized tools help achieve this precision. Cutting foam tools, like hot wire cutters and CNC machines, offer automated and efficient solutions. These tools reduce manual labor and improve productivity. Advanced features ensure consistent and high-quality results. Using the right tool saves time and effort. Foam saws handle thick materials with ease. This efficiency enhances your work quality. Embrace these tools for better foam cutting experiences.
Understanding Cutting Foam Tools
Cutting foam tools are essential for anyone working with foam materials. These tools help you achieve precise and clean cuts, whether you’re working on artistic projects, upholstery, or industrial applications. Let’s explore the different types of cutting foam tools and how to choose the right one for your project.
Types of Cutting Foam Tools
Hot Wire Cutters
Hot wire cutters use a heated wire to slice through foam. This tool is perfect for creating smooth and straight cuts. The heat melts the foam as the wire passes through, reducing mess and ensuring precision. Hot wire cutters are ideal for projects requiring intricate shapes and designs.
Electric Knives
Electric knives offer a versatile option for cutting foam. These knives have serrated blades that move back and forth rapidly. This motion allows for quick and efficient cutting. Electric knives work well for both straight and curved cuts. You can use them for various foam densities and thicknesses.
CNC Foam Cutters
CNC foam cutters provide automated precision. These machines use computer-controlled movements to cut foam into specific shapes and sizes. CNC foam cutters are excellent for large-scale projects. They ensure consistent quality and reduce material wastage. Industries like packaging and automotive often rely on CNC foam cutters for their precision needs.
Choosing the Right Cutting Foam Tool for Your Project
Selecting the right cutting foam tool depends on several factors. Consider the type of foam you’re working with and the complexity of your design. Each tool offers unique features that cater to different project requirements.
Factors to Consider
- Foam Type: Different foams require specific tools. Soft foams may need electric knives, while denser foams benefit from hot wire cutters.
- Project Scale: Large projects might require CNC foam cutters for efficiency. Smaller tasks could be handled with electric knives or hot wire cutters.
- Precision Needs: Intricate designs demand precise tools like CNC foam cutters. For basic shapes, electric knives or hot wire cutters suffice.
Comparing Tool Features
When comparing cutting foam tools, focus on key features:
- Blade or Wire Quality: High-quality blades or wires ensure clean cuts.
- Ease of Use: User-friendly tools enhance productivity.
- Safety Features: Look for tools with safety mechanisms to protect users.
Choosing the right cutting foam tool enhances your project’s outcome. By understanding the types of tools available and considering your specific needs, you can make informed decisions that lead to successful foam cutting experiences.
Techniques for Precise Foam Cutting
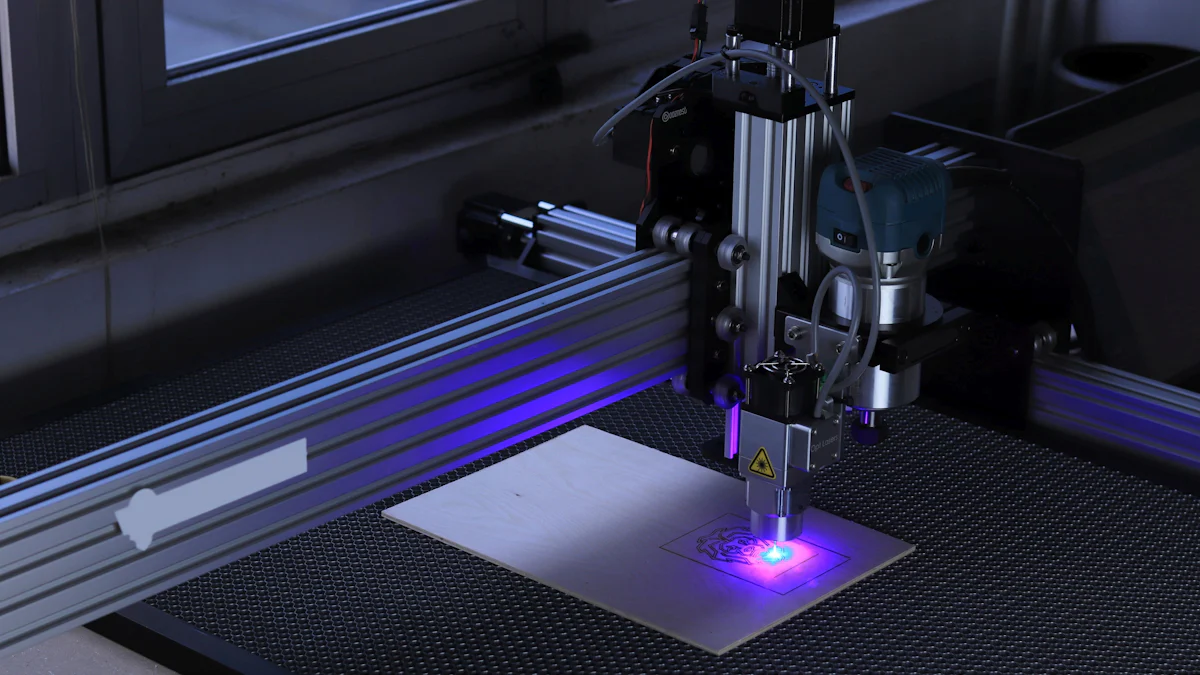
Cutting foam tools offer a variety of techniques to achieve precise results. Let’s dive into how you can prepare and cut foam with accuracy.
Preparing the Foam
Proper preparation sets the stage for successful cutting. Follow these steps to get your foam ready.
Measuring and Marking
Accurate measurements ensure clean cuts. Use a ruler or measuring tape to mark your cutting lines. A pencil or marker works well for marking. Double-check your measurements before proceeding. This step prevents mistakes and saves material.
Securing the Foam
Secure foam to prevent movement during cutting. A stable surface is essential. Use clamps or weights to hold foam in place. This stability allows for smoother cuts. Ensure foam does not shift while you work.
Cutting Techniques
Different projects require different cutting techniques. Here are some methods to consider when using cutting foam tools.
Straight Cuts
Straight cuts are common in many projects. Use a straightedge as a guide. Align your cutting tool with the marked line. Apply steady pressure for a clean cut. Hot wire cutters excel at straight cuts due to their precision.
Curved Cuts
Curved cuts add a creative touch to your projects. Electric knives handle curves well. Move the knife in a gentle arc. Keep a steady hand to maintain control. Practice on scrap foam to perfect your technique.
Intricate Designs
Intricate designs require advanced cutting foam tools. CNC machines shine in this area. These machines follow computer-generated paths. Achieve complex shapes with ease. CNC technology opens doors to detailed and customized designs.
Cutting foam tools have evolved with technological advancements. CNC machines and hot wire cutters enhance precision and efficiency. Industries like automotive and packaging benefit from these tools. The ability to create intricate designs has expanded possibilities. Embrace these techniques to elevate your foam cutting skills.
Tips for Maintaining Foam Cutting Tools
Proper maintenance keeps cutting foam tools in top shape. Regular care extends the life of your equipment. Well-maintained tools deliver precise results every time. Let’s dive into some essential tips for keeping your tools in excellent condition.
Cleaning and Storage
Cleaning and storing tools correctly ensures they remain efficient and safe. Follow these steps to maintain your cutting foam tools.
Cleaning Blades and Wires
Clean blades and wires after each use. Foam residue can build up and affect performance. Use a soft brush or cloth to wipe away debris. For stubborn residue, apply a mild detergent solution. Rinse thoroughly and dry completely to prevent rust.
Proper Storage Practices
Store cutting foam tools in a dry, cool place. Moisture can cause rust and damage. Use protective cases or covers to shield tools from dust. Keep blades and wires separate to avoid dulling. Organized storage makes finding tools easier and prevents accidents.
Regular Maintenance
Routine maintenance keeps cutting foam tools sharp and ready for action. Implement these practices to ensure peak performance.
Sharpening Blades
Sharp blades cut foam cleanly and efficiently. Dull blades require more effort and can damage foam. Use a sharpening stone or tool designed for your blade type. Follow the manufacturer’s instructions for best results. Regular sharpening saves time and improves cut quality.
Checking for Wear and Tear
Inspect cutting foam tools regularly for signs of wear. Look for nicks, bends, or other damage. Replace worn parts promptly to maintain precision. Regular checks prevent unexpected breakdowns and ensure safety.
Cutting foam tools are essential for achieving precise results. Proper maintenance enhances their performance and longevity. Clean, store, and maintain your tools diligently. These practices keep your equipment in top condition and ready for any project.
Precision in foam cutting transforms your projects. Specialized tools like hot wire cutters and CNC machines offer accuracy. Practicing different techniques improves your skills. Experiment with various methods to find what works best for you. Regular maintenance keeps your tools in top condition. Clean and sharpen blades often. Store tools properly to extend their life. Well-maintained tools ensure consistent results. Embrace these practices for long-term success. Your projects will benefit from the care and attention you give your tools.