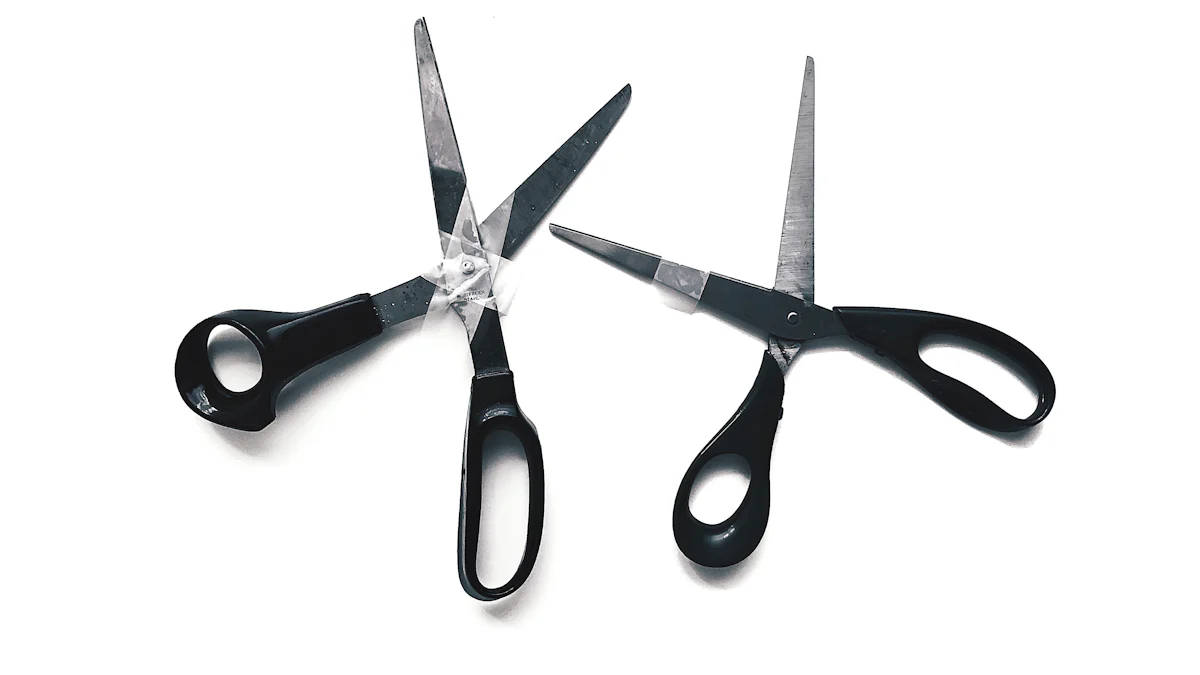
Selecting the right tin cutting tools ensures precision and efficiency in your projects. Proper tools reduce harmful kickback, enhancing safety and productivity. Factors like blade material and handle design influence your choice. Tool durability increases by five times with quality materials. Machining efficiency improves more than two times with the right tools. Understanding these factors helps you make informed decisions for better results.
Understanding Tin Cutting Tools
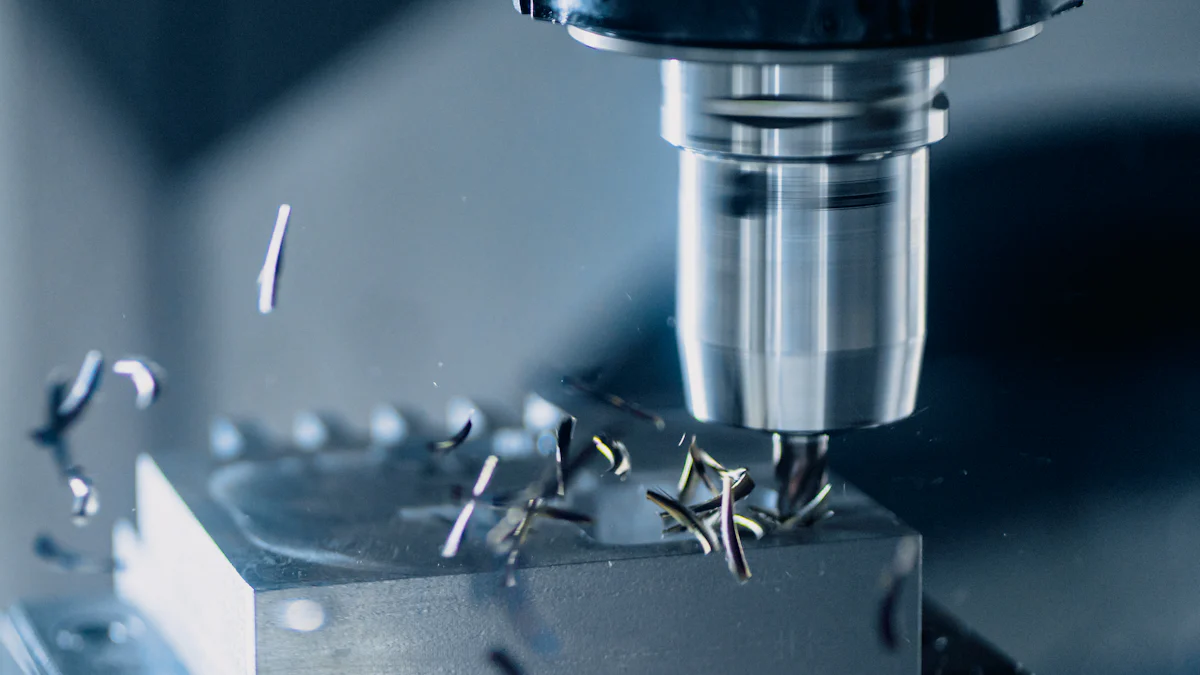
Types of Tin Cutting Tools
Manual Tin Snips
Manual tin snips resemble heavy-duty scissors. These tools work well for cutting sheet metal, gutters, and metal roofing. Straight-cutting snips create long, straight lines. Curved blades allow for circular shapes. Beginners often choose manual tin snips for control and precision. These tools help practice basic cutting techniques.
Electric Tin Shears
Electric tin shears offer speed and efficiency. These tools cut through metal with ease. The motorized action reduces physical effort. Electric shears suit large projects. These tools handle thicker metals better than manual options. Users find electric shears ideal for repetitive tasks.
Pneumatic Tin Cutters
Pneumatic tin cutters use compressed air. These tools provide powerful cutting action. Pneumatic cutters excel in industrial settings. They cut through tough materials quickly. The air-powered mechanism ensures consistent performance. Pneumatic cutters require an air compressor. These tools are best for professional use.
Features to Consider
Blade Material
Blade material affects cutting performance. High-quality steel blades last longer. Steel resists wear and tear. Serrated blades grip the material better. Smooth blades suit thin metals. Blade choice impacts precision and ease of use.
Handle Design
Handle design influences comfort. Ergonomic handles reduce hand strain. Rubber grips provide better control. Handle size should match hand size. Proper design enhances leverage. Comfortable handles improve cutting accuracy.
Cutting Capacity
Cutting capacity determines tool suitability. Different tools handle various metal thicknesses. Check specifications before purchasing. Ensure the tool matches your project needs. Cutting capacity affects efficiency and safety.
Factors to Consider When Choosing Tin Cutting Tools
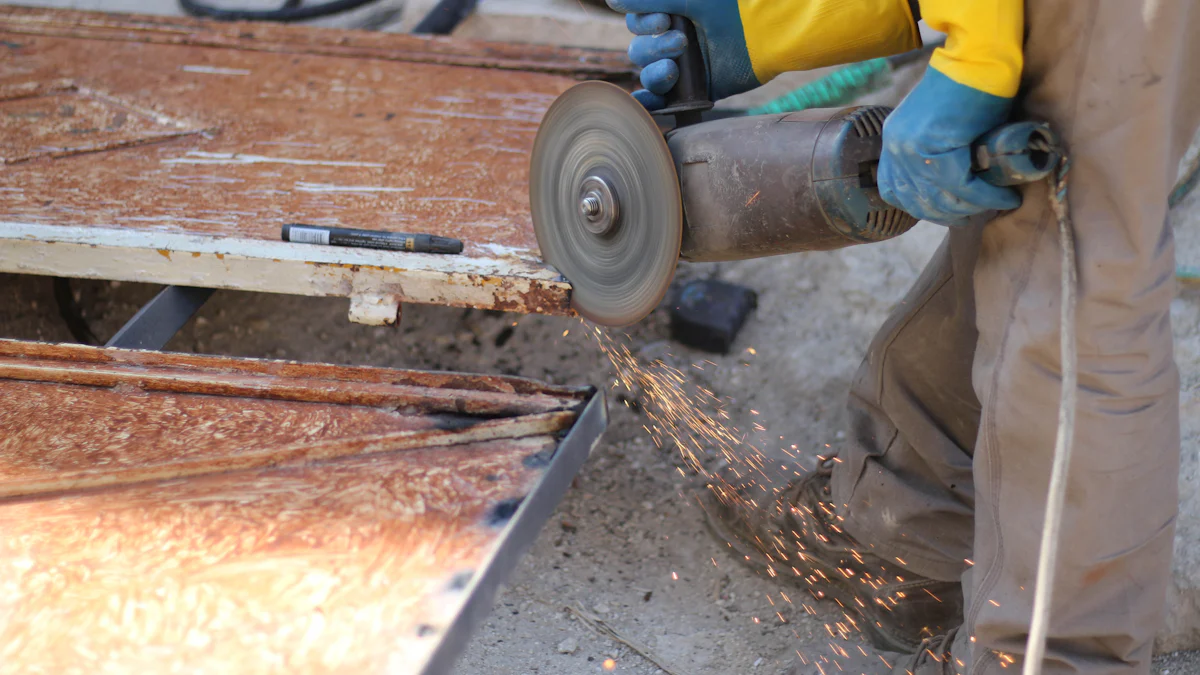
Choosing the right tin cutting tools involves understanding specific use cases and ergonomic factors. Each project requires a different approach to ensure efficiency and safety.
Specific Use Cases
Home DIY Projects
Home DIY projects often involve lighter materials. Tin cutting tools for these tasks should offer precision and ease of use. Manual tin snips work well for small-scale projects. These tools provide control for detailed cuts. Electric tin shears can also be beneficial. The motorized action reduces physical strain during extended use. Selecting the appropriate tool enhances project outcomes and user satisfaction.
Professional Metalwork
Professional metalwork demands robust tin cutting tools. Pneumatic tin cutters excel in industrial settings. These tools handle thicker metals with ease. Consistent performance is crucial for professional tasks. High-quality steel blades ensure durability and accuracy. Ergonomic designs reduce fatigue during long hours of work. Choosing the right tool improves workflow and decreases costs.
Ergonomics and Comfort
Ergonomics play a vital role in selecting tin cutting tools. Comfortable tools enhance user experience and productivity.
Weight and Balance
Weight and balance affect tool handling. Lightweight tools reduce arm fatigue. Balanced designs provide better control. Proper weight distribution enhances cutting precision. Users should test tools for comfort before purchasing. A well-balanced tool increases efficiency and safety.
Grip and Handle Comfort
Grip and handle comfort impact user satisfaction. Rubber grips offer better control. Ergonomic handles fit various hand sizes. Comfortable handles reduce hand strain. Proper grip design enhances leverage. Users should prioritize comfort to improve cutting accuracy.
Recommendations and Best Practices
Maintenance Tips
Proper maintenance of tin cutting tools ensures long-lasting performance and reliability. Regular care prevents wear and tear, keeping tools in optimal condition.
Cleaning and Lubrication
Clean your tin cutting tools after each use. Remove any metal shavings or debris to prevent rust and corrosion. Use a soft cloth or brush for cleaning. Apply a light coat of oil to the blades. Lubrication reduces friction and enhances cutting efficiency. Well-maintained tools offer smoother operation and longer life.
Proper Storage
Store tin cutting tools in a dry place. Moisture can cause rust and damage. Use a toolbox or storage case for organization. Keep tools away from direct sunlight and extreme temperatures. Proper storage maintains tool integrity and readiness for future projects.
Safety Considerations
Safety should always be your top priority when using tin cutting tools. The process can produce sharp edges and flying debris. Follow essential safety measures to protect yourself.
Protective Gear
Wear appropriate protective gear during cutting tasks. Use safety goggles to shield your eyes from debris. Gloves protect your hands from sharp edges. Ear protection is necessary when using power tools. Protective gear minimizes the risk of injury.
Safe Handling Techniques
Practice safe handling techniques with tin cutting tools. Maintain a firm grip on the tool. Keep your fingers away from the cutting edge. Use steady pressure for clean cuts. Avoid forcing the tool through the material. Safe handling ensures precision and reduces accidents.
Expert Testimony:
“Safety should always be your top priority when cutting metal. The process can produce sharp edges, flying debris, and intense heat.”
Remember, proficiency in using tin cutting tools takes practice and patience. With proper maintenance and safety measures, you can achieve exceptional results in your projects.
Selecting the right tin cutting tools ensures efficient and accurate results. Quality tools offer better performance and durability. Investing in high-quality tools enhances safety features. Assess personal needs before purchasing. Consider specific project requirements. Evaluate tool features and ergonomics. Balance cost and quality for optimal outcomes. Seek expert recommendations for improved project success. Proper tool selection impacts cutting process quality. Make informed decisions to achieve exceptional results in your projects.