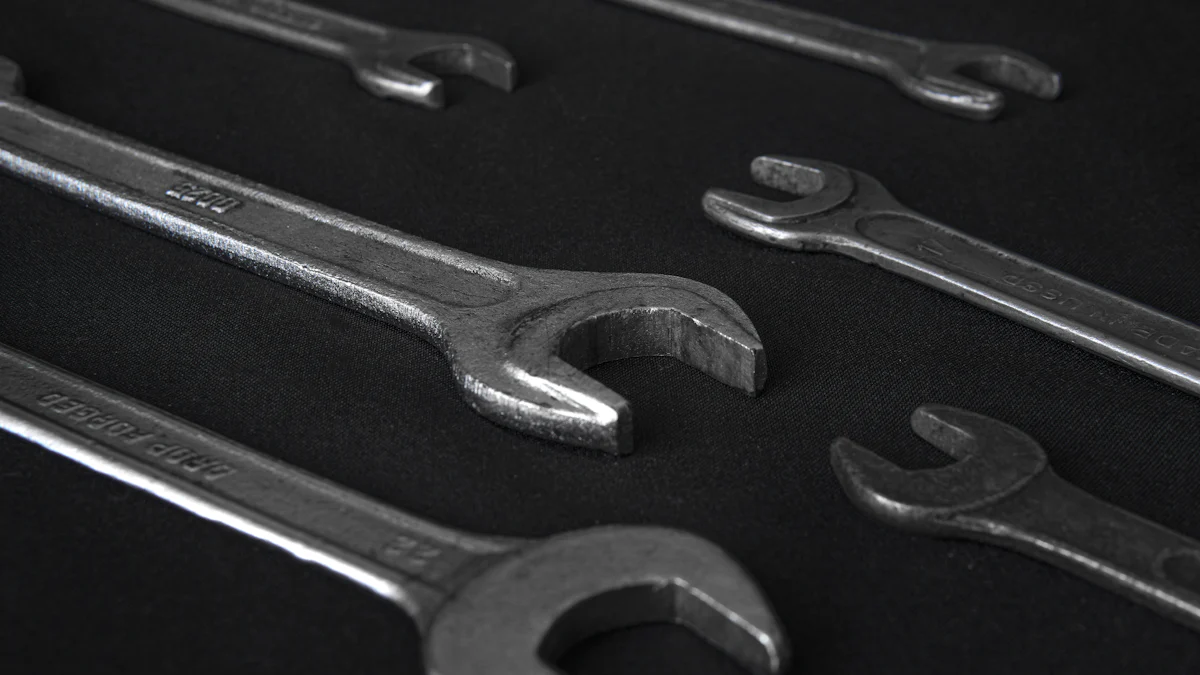
Ratchet spanners play a crucial role in various mechanical tasks. Selecting the appropriate type ensures efficiency and safety. The 6 point ratchet spanner is designed to handle higher torque due to its larger teeth and more material grip. The 12-point design offers versatility by fitting fasteners at multiple angles. Understanding the differences between these tools can help users make informed decisions for their specific needs.
Understanding 6-Point Ratchet Spanners
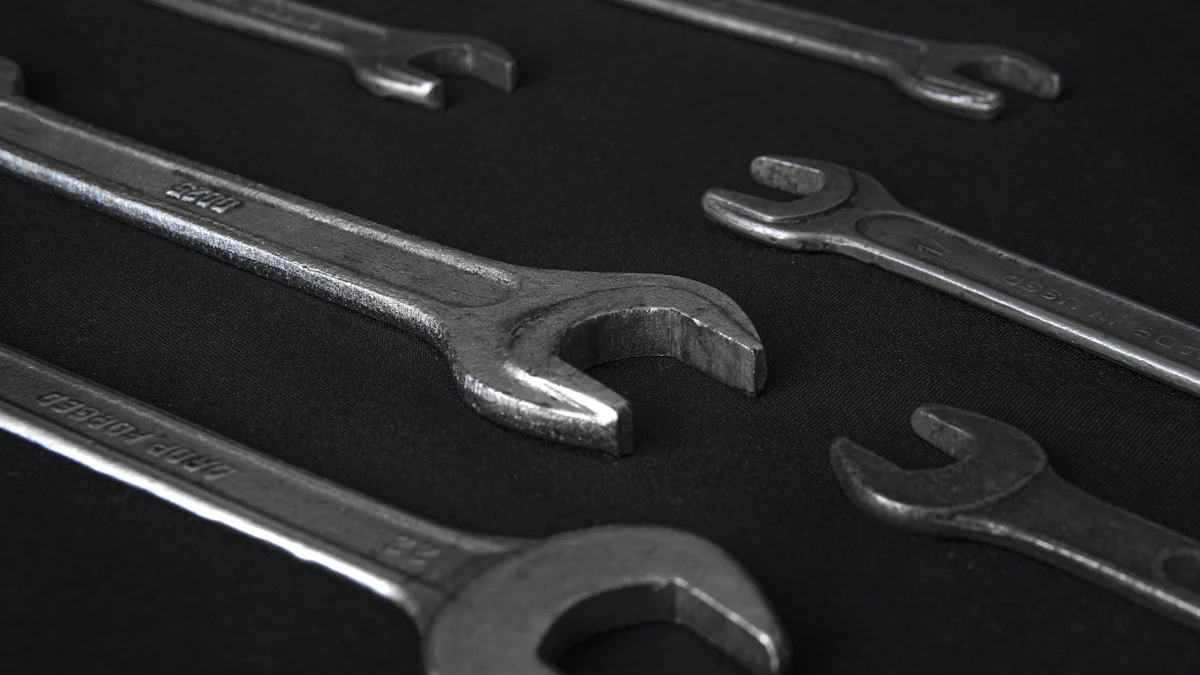
Design and Structure
Number of contact points
The 6 point ratchet spanner features six contact points. These points engage with the fastener head. This design provides a more secure grip. The increased contact area reduces the risk of slippage. This feature makes the 6 point ratchet spanner ideal for high-torque applications.
Material and build quality
Manufacturers often use high-strength steel to construct 6 point ratchet spanners. This choice of material ensures durability. The robust build quality allows the tool to withstand significant torque. Users can rely on the 6 point ratchet spanner for demanding tasks.
Applications and Use Cases
Common scenarios for use
The 6 point ratchet spanner excels in automotive repair. Mechanics prefer this tool for loosening and tightening bolts. The secure grip minimizes the risk of damaging fasteners. This tool also finds use in heavy machinery maintenance. The ability to handle high torque makes it indispensable in these settings.
Advantages in specific tasks
The 6 point ratchet spanner offers several advantages. The tool’s design reduces the likelihood of rounding off bolt heads. This feature proves beneficial when dealing with stubborn or rusted fasteners. The spanner’s ability to grip damaged bolts enhances its utility. Users find this tool particularly useful in challenging conditions.
Benefits
Durability
Durability stands out as a key benefit of the 6 point ratchet spanner. The high-quality materials used in its construction ensure a long lifespan. Users can expect consistent performance over time. This reliability makes the tool a valuable addition to any toolkit.
Torque distribution
The 6 point ratchet spanner excels in torque distribution. The six contact points evenly distribute the applied force. This feature reduces stress on individual points. The result is a more efficient transfer of torque. Users can achieve higher torque levels without compromising the fastener.
Understanding 12-Point Ratchet Spanners
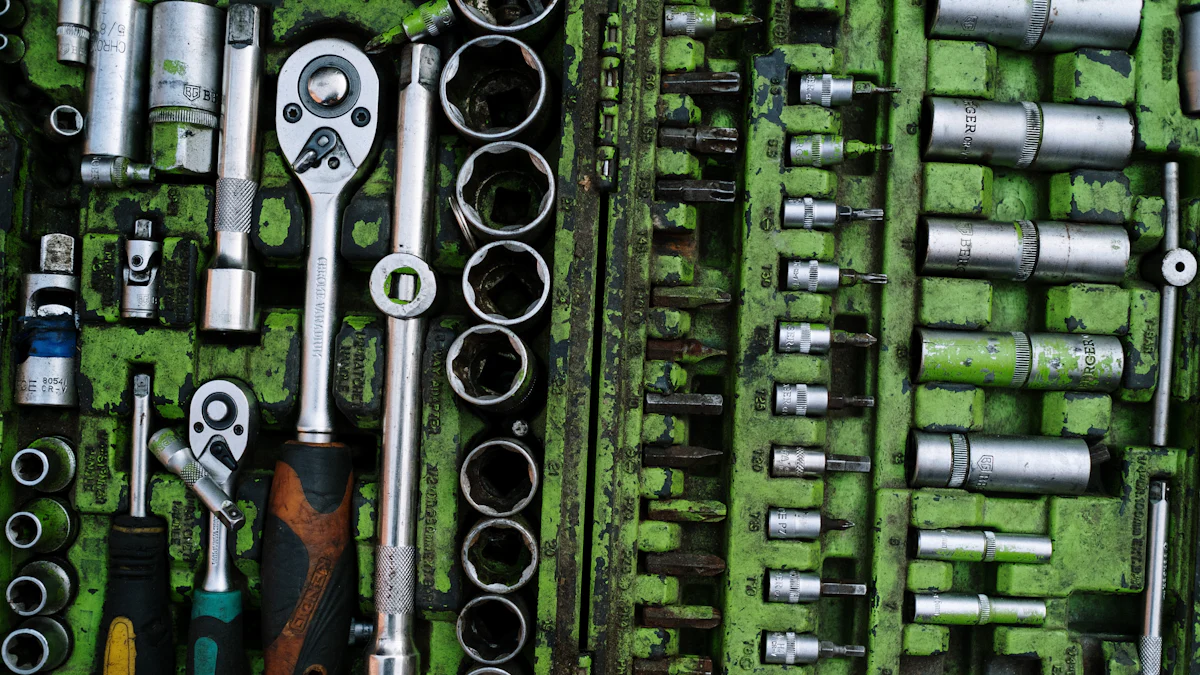
Design and Structure
Number of contact points
The 12-point ratchet spanner features twelve contact points. These points engage with the fastener head at multiple angles. This design allows for more flexibility in positioning. Users can connect the tool to the fastener in tighter spaces. The increased number of contact points provides versatility.
Material and build quality
Manufacturers often use high-strength steel to construct 12-point ratchet spanners. This choice ensures durability and reliability. The robust build quality allows the tool to handle moderate torque levels. Users can trust the 12-point ratchet spanner for various tasks. The construction quality ensures a long lifespan.
Applications and Use Cases
Common scenarios for use
The 12-point ratchet spanner excels in situations requiring flexibility. Mechanics often use this tool in automotive repair. The ability to engage fasteners at multiple angles proves beneficial. Users find the 12-point ratchet spanner useful in tight spaces. This tool also finds applications in general maintenance tasks.
Advantages in specific tasks
The 12-point ratchet spanner offers several advantages. The design reduces the need for precise alignment. Users can quickly engage the fastener without much adjustment. This feature proves useful in confined areas. The tool’s versatility enhances its utility in various tasks. Users appreciate the ease of use in challenging conditions.
Benefits
Versatility
Versatility stands out as a key benefit of the 12-point ratchet spanner. The multiple contact points allow for flexible positioning. Users can engage fasteners from different angles. This feature makes the tool suitable for various applications. The 12-point ratchet spanner adapts to different scenarios with ease.
Ease of use in tight spaces
Ease of use in tight spaces is another significant benefit. The 12-point design allows for quick engagement. Users can work efficiently in confined areas. The tool’s ability to fit into small spaces enhances its practicality. This feature makes the 12-point ratchet spanner indispensable for certain tasks.
Comparative Analysis
Performance
Torque handling
The 6 point ratchet spanner excels in torque handling. The design features larger teeth and more material grip. This allows the tool to withstand higher torque amounts. Users can apply significant force without risking damage to the fastener. In contrast, the 12-point ratchet spanner handles moderate torque levels. The smaller engagement areas make it suitable for light-duty jobs. The choice between these tools depends on the torque requirements of the task.
Slippage risk
The 6 point ratchet spanner minimizes slippage risk. The six contact points provide a secure grip on the fastener head. This reduces the chances of rounding off bolt heads. Users find this feature beneficial when dealing with stubborn or rusted fasteners. The 12-point ratchet spanner has a higher slippage risk due to its design. The increased number of contact points offers less grip. This makes the tool less ideal for high-torque applications.
Practicality
Ease of use
Ease of use varies between the two types of ratchet spanners. The 6 point ratchet spanner requires precise alignment with the fastener. This can make it challenging to use in confined spaces. However, the secure grip compensates for this drawback. The 12-point ratchet spanner offers more flexibility in positioning. Users can engage the fastener at multiple angles. This makes the tool easier to use in tight spaces.
Versatility in different tasks
Versatility is a key advantage of the 12-point ratchet spanner. The multiple contact points allow for flexible positioning. Users can engage fasteners from different angles. This makes the tool suitable for various applications. The 6 point ratchet spanner excels in specific tasks requiring high torque. The secure grip and reduced slippage make it ideal for demanding jobs. The choice between these tools depends on the specific requirements of the task.
Cost and Value
Price comparison
Price comparison reveals differences between the two types of ratchet spanners. The 6 point ratchet spanner often costs more due to its robust build quality. The high-strength materials used in its construction contribute to the higher price. The 12-point ratchet spanner generally costs less. The design focuses on versatility rather than high torque handling. Users should consider their budget when choosing between these tools.
Long-term value
Long-term value depends on the durability and performance of the tool. The 6 point ratchet spanner offers excellent long-term value. The high-quality materials ensure a long lifespan. Users can rely on consistent performance over time. The 12-point ratchet spanner also provides good value. The versatility and ease of use make it a valuable addition to any toolkit. The choice between these tools should consider both immediate needs and long-term benefits.
The 6-point ratchet spanner excels in high-torque applications due to its secure grip and durability. The robust build quality ensures a long lifespan, making it ideal for demanding tasks. The 12-point ratchet spanner offers versatility and ease of use in tight spaces. The multiple contact points allow for flexible positioning, making it suitable for various applications.
Expert Testimony: “A 12-point socket or wrench is most for any light-duty jobs that you may have from day to day but it doesn’t mean that it is any better than the 6 point.”
For those needing a tool for high-torque tasks, the 6-point ratchet spanner proves superior. For versatility and ease of use in confined areas, the 12-point ratchet spanner stands out.
See Also
Scooter Upgrades: High-Quality Parts for Optimal Performance
Discovering a Range of Sock Options for Both Genders